皆さんはクルマの生産工場でどんな人々が働いているか、想像したことはありますか?根っからのクルマ好きな人でしょうか。重い部品なども扱うことから、男性が多い職場という印象をお持ちかもしれません。
確かに、かつては力仕事などを伴う製造ラインでの仕事は主に男性が行っていました。しかし、「工場=男性の職場」というのは遠い昔の話で、工場で活躍する女性は年々増えています。日産では、老若男女を問わず、誰もがより少ない負担で、安全に働ける工場づくりを目指しています。
今回は、日産栃木工場の鋳造ラインの中でも、女性従業員数が約2割にアップしたシリンダーヘッドの新ラインでの取り組みをご紹介します。そこには、「誰もが働ける工場を」という熱い想いがありました。
クルマづくりの要、鋳造部門
栃木県河内郡に位置する日産の栃木工場。1968年にアルミ・鉄の鋳造工場として操業を開始し、1971年には車両の組立工場も完成。現在は「GT-R」や「フェアレディZ」など、日産の代表的なクルマを生産する歴史のある工場です。一方で、取り巻く様々な環境の変化に対応した「ニッサン インテリジェント ファクトリー」が導入され、最新のEV「日産アリア」を生産する、クルマづくりの最先端を行く工場でもあります。
この栃木工場の中でも、工場全体の4分の1ほどにあたり、東京ドーム約5個分という大きな敷地面積を誇るのが鋳造部門。鋳造とは、アルミや鉄などの金属を溶かし、成形して部品を作る工程のことで、特にクルマのエンジンパーツなどにとって重要な工程です。
鋳造ラインではシリンダーヘッドなど、10kgを超える重量のある部品を製造しています。その製造過程では高温での金属の溶解や有機物の取扱いも必要なため、工場の中でも特に安全への配慮が必要とされ、他のラインと比べてCO2排出量が多いことも課題となっていました。
その鋳造ラインがどのようにして、女性が働きやすく、かつ環境に優しいラインへと生まれ変わったのでしょうか?
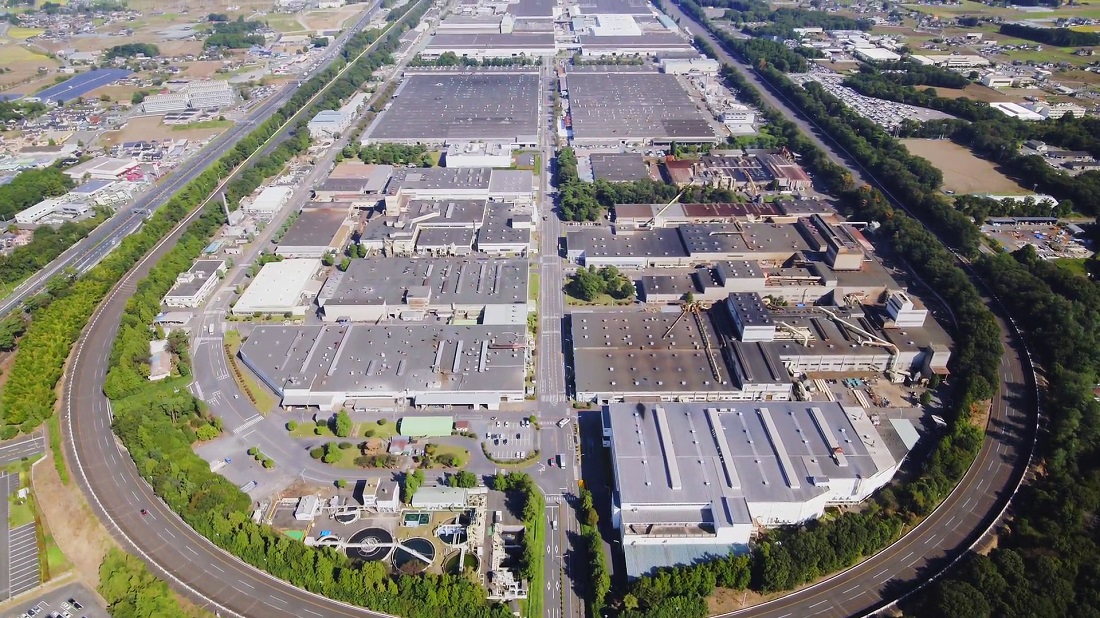
「誰もが働けるラインにする」という熱い想い
「2018年頃、鋳造ラインを刷新するプロジェクトが立ち上がりました。刷新後のラインは、環境にやさしく、力仕事が苦手な人を含め、性別や年齢を問わずに誰でも働けるラインにしなければならない。ですから、実際に働く女性の意見も取り入れながら、強い意志をもって改善に取り組みました。」と語るのは、栃木工場でラインの設計を担当する土屋 真一。
そんな熱い想いが実現した新しい鋳造ラインをご紹介しましょう。
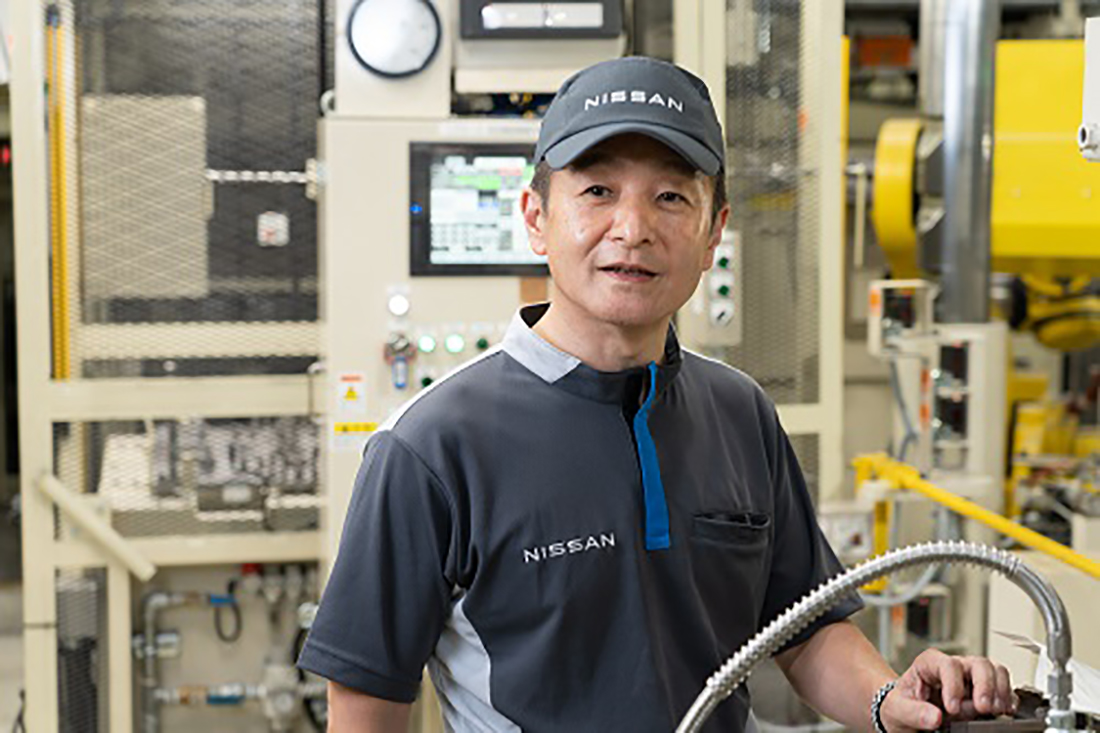
鋳造ライン設計 土屋 真一
明るくクリーンな職場に刷新
職場に入ってすぐ気が付くのは、明るくクリーンな雰囲気です。
シリンダーヘッドは、部品の内側に空洞を作るために中子という砂の型を金型の中にセットし、そこに溶けたアルミを流し込んで成型します。従来は、有機素材の粘結材で砂を固めて中子をつくっていたため、鋳造時の熱で中子が焼かれる際に発生する有機ガスと臭いを回収し、浄化するための設備が天井を覆っていました。今回、中子の粘結材を無機素材に変更したことで、有機ガスや臭いの発生がないクリーンな環境を実現し、天井の設備も不要となりました。
さらに、省エネで輝度の高いLED照明を導入し、床の塗装も一新したことで、明るく環境に優しい職場へと生まれ変わったのです。
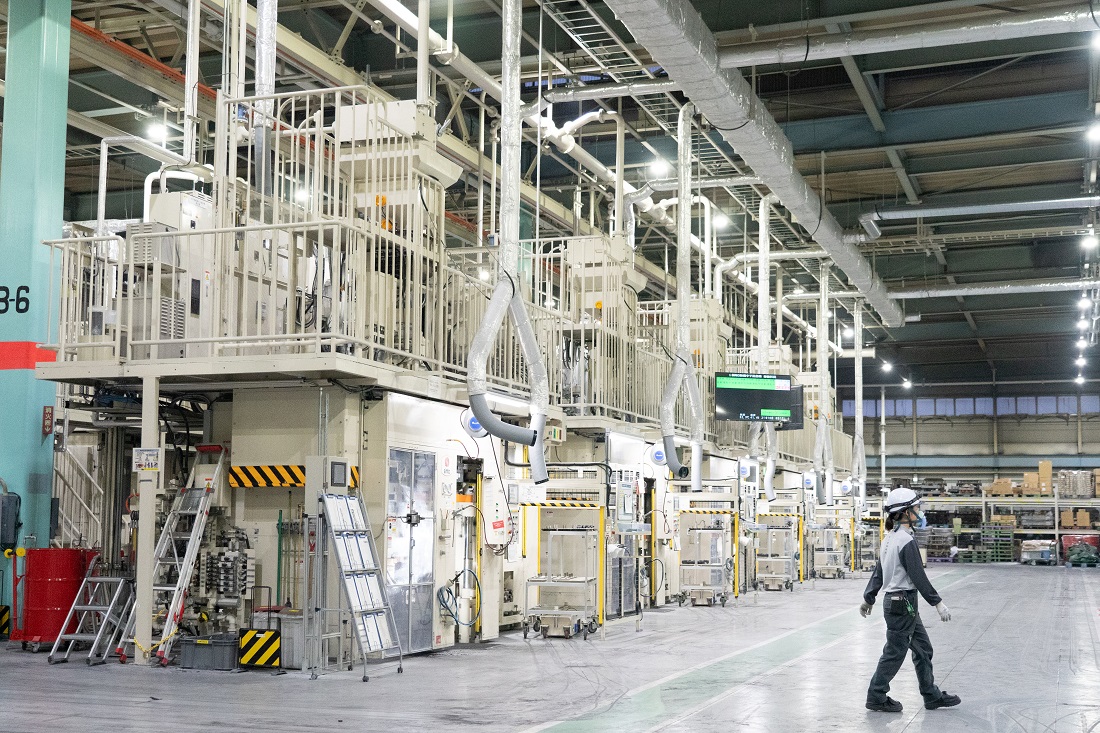
最新機械の導入で大幅な負担軽減
安全性や作業負荷の面でも、大きな改善を実現しました。
まず、ラインから離れた溶解炉でアルミを溶かし、高温になったアルミをフォークリフトで鋳造機まで運搬するという作業を見直しました。鋳造機のそばでアルミを溶解する手元溶解炉を導入したのです。これで、高温のアルミを運搬する作業が不要となりました。さらに、必要なときに必要な分だけ溶解することで、エネルギーの消費も抑えることが可能となりました。
次に、最終出荷前にシリンダーヘッドの内部を検査する作業に、最新の機器を導入しました。これまでは、複雑な形状をしたシリンダーヘッドの中に内視鏡を差し込み、中子折れや砂残りがないか、一つ一つを目で確認していました。これは非常に高い技能と集中力を要する作業です。そこに、内部を自動で確認できるCT(コンピュータ断層撮影)を導入することで、作業負荷を大きく軽減し、作業時間も短縮しました。
また、外観の検査では、これまでは約10kg以上あるシリンダーヘッドを手で持ち上げて、回転させながら目視チェックしていました。しかし、シリンダーヘッドを自動反転できるマシンを導入したことで、無理なく確実に作業ができるようになりました。
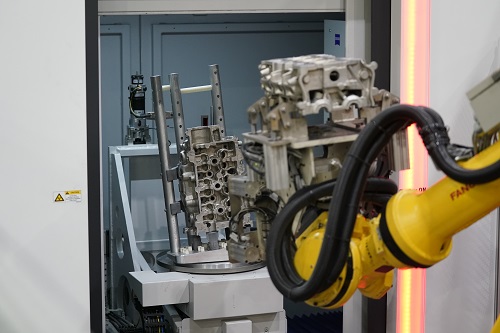
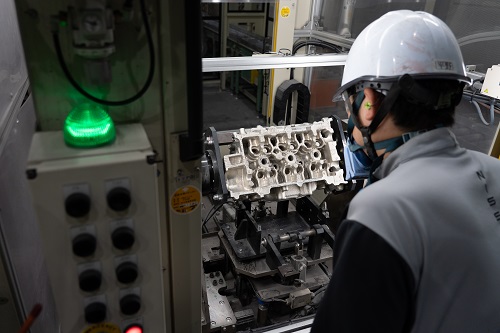
CO2削減で環境にもやさしく
もう一つの大きなポイントは、環境への対応です。高温処理等を必要とする鋳造ラインは、工場全体のCO2排出量の約6割を占めており、その削減が大きな課題となっていました。今回、シリンダーヘッド鋳造ラインを刷新したことで、シリンダー製品1個あたり24%、さらに熱処理過程では41%のCO2排出量を削減しました。(対前年度比)
今回、CO2排出量の削減に大きく貢献した熱処理工程は、成形後のシリンダーヘッドに強度を与えるための工程です。バスケットに多くのシリンダーヘッドを入れて、同時に熱処理炉内に投入する従来の方法では、バスケットも熱することになり、余分な熱量が発生していました。今回、バスケットを使わず、シリンダーヘッドを一つずつ投入するロータリー熱処理炉に変更したことで、必要な部品だけを効率的に熱処理することが可能となったのです。
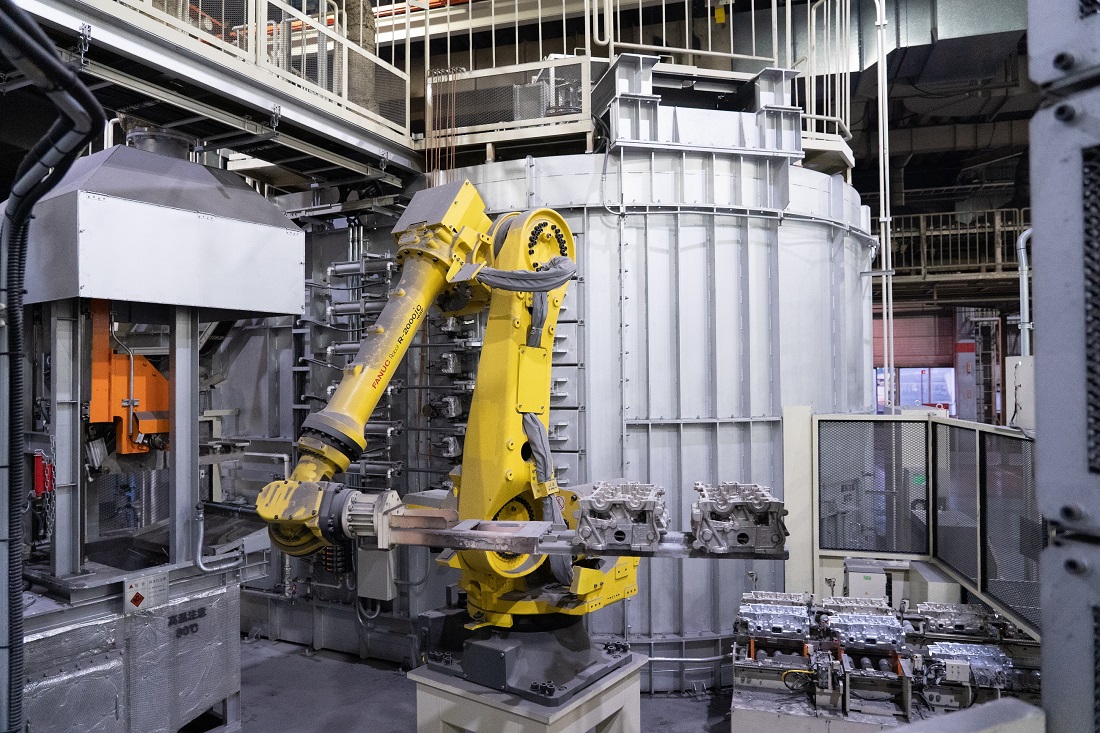
チームで改善を実現、仕事の後のプライベートも変化
さて、人にも環境にもやさしい職場は、どのように実現したのでしょうか。
「栃木工場には部門や工程を越えてワンチームで課題に取り組む力があります。」と自信を見せるのは、今回のライン刷新に携わった永森 陽介。工場内の課題を皆で協力して解決するチーム力が、今回の改善につながったと語ります。
鋳造ラインで働く津川 加奈は、「職場が明るくなり、作業負担も軽減され、本当に働きやすくなりました」と笑顔を見せてくれました。職場の変化は、彼女の私生活にも変化をもたらしているとか。「臭いがついていないかなどと気にする必要がなくなりました。だから、仕事が終わったあと、すぐ気軽に外出できるんです」
変わりゆくものづくりの現場。最高の一台をお客さまにお届けするため、皆が笑顔で仕事に取り組んでいます。
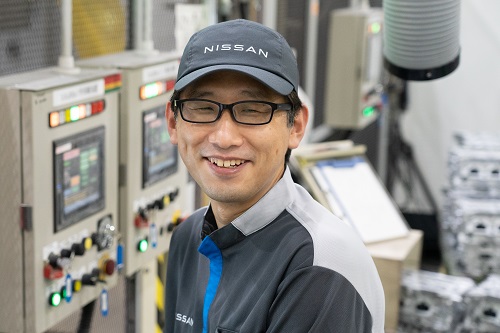
鋳造技術エンジニア 永森 陽介
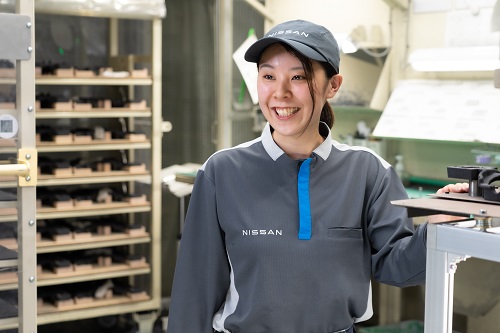
鋳造ライン担当 津川 加奈
カーボンニュートラルに向けて
日産は、2050年までにクルマのライフサイクル全体*1でカーボンニュートラルを実現する目標を定めています。栃木工場における「ニッサン インテリジェント ファクトリー」の導入はこの取り組みの一つの柱でもあり、車両組み立て時の生産効率を向上させるイノベーションの推進、生産におけるエネルギーと材料の効率向上を進めています。
ライン全体の責任者である西 高宏は、「日産の工場は、自動化や効率化が進んでいます。しかし、まだまだゴールではありません。今後もずっと、進化する工場であり続ける。そのために、これからも私たちは日々、改善を続けていきます」と力を込めました。
誰もが生き生きと働ける、よりクリーンで安全でインクルーシブな工場へ。さらなる進化への挑戦は続きます。
- クルマのライフサイクルには、原材料の採掘から、生産、クルマの使用、使用済み自動車のリサイクルや再利用までを含みます。
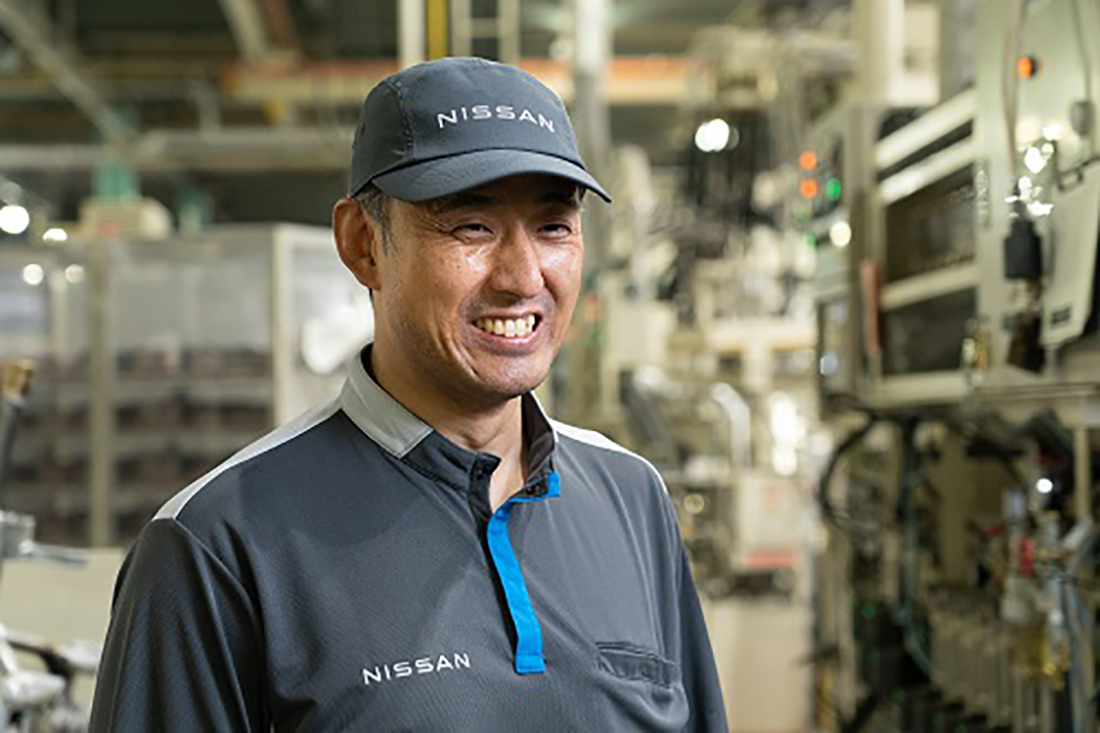
鋳造ラインマネージャー 西 高宏
シリンダーヘッド鋳造の流れ
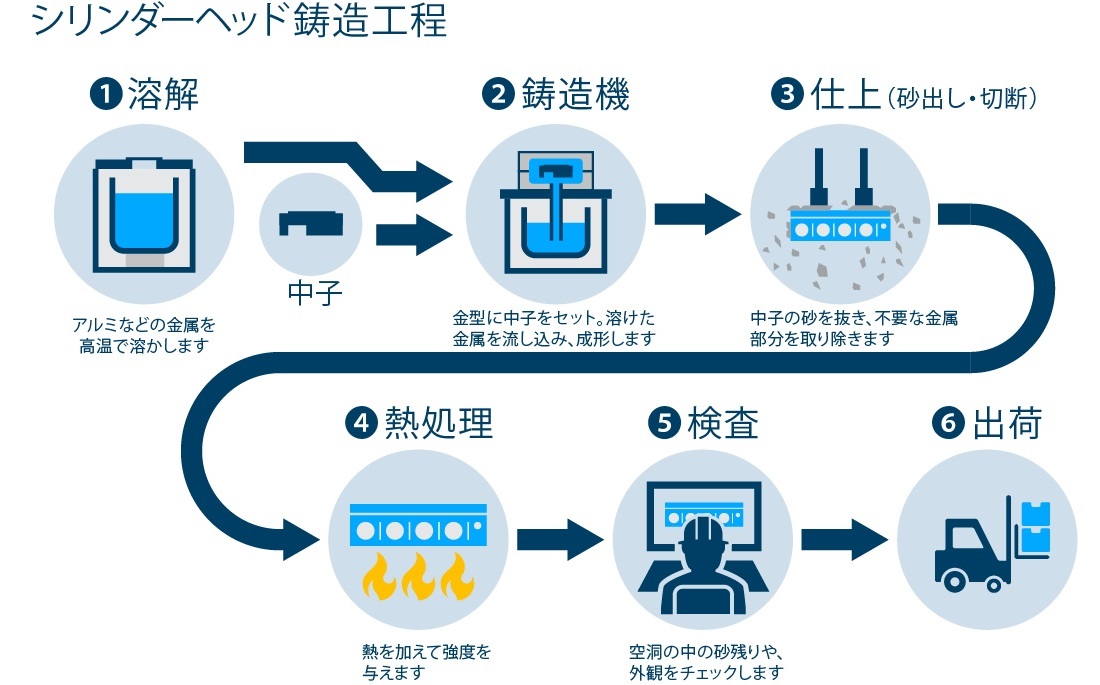