2020年に栃木工場への導入を皮切りに、国内外の工場へ展開が予定されている「ニッサン インテリジェント ファクトリー」は別の日産ストーリーズでご紹介しましたが、日産は生産現場の改善に常に取り組んでいます。この改善は、最新の技術を搭載したクルマの生産体制を作るためだけではなく、作業を自動化し、作業員にかかる負荷を軽減することでより良い職場環境を実現するためでもあります。
「未来のクルマは人がつくるもの」。クルマを生産する上でロボットの役割がどれだけ増えたとしても、人が生産現場からいなくなることはありません。特に部品の取り付けや製品の品質チェックなど、まだまだ人に頼らなければならない作業が多くあります。日産は、生産効率を上げるためだけではなく、工場で働く人たちの肉体的な負担や精神的な負担を軽減するためにロボットを導入し、職場環境の改革に取り組んでいます。今回はその一部を紹介しましょう。
「ニッサン インテリジェント ファクトリー」による自動化推進
組立ラインには、作業者の肉体的な負担を軽減することが難しい作業が数多くありますが、その一つがヘッドライニング(天井の内張り)の取り付けです。これまでは作業員が車内に乗り込み、腰を曲げた状態でヘッドライニングの取り付け作業をしています。さらに「ニッサン インテリジェント モビリティ」に欠かせないカメラやレーダー、スイッチ等の各種デバイスの取り付けが増え、作業が複雑化しました。そこで日産は、ヘッドライニングの取り付けを自動化することにチャレンジしていきます。
設備の自動化を担当するエンジニアリング部門で働いている阿部 浩二 主担は、「ヘッドライニングの取り付けは肉体的に大変な仕事です。自動化に向けて何年も開発とテストを重ねてきました。このように自動化を進めることによって、作業員の方々には、人が作業することによってさらに付加価値を付けられるような役割を任せることができます」と語ります。
さらに、工程ごとにクオリティーゲートを投入し、各工程の品質を自動判定することで人による誤判定を防止することによって、作業員の肉体的および精神的な負担も軽減しつつ、お客さまに品質を保証したクルマをお届けすることを実現します。例えば、クルマの走行や停止に影響する400点以上のトルクの締結作業を、自動判定装置でモニタリングし、常に正確な精度が維持されていることを保証します。さらに最終検査では、音声での認証システムを導入し、資格を持った検査員のみによる品質保証の仕組みを構築します。
人とロボットの共生
溶接や組み立てなどの作業を行う従来型の産業用ロボットは、その大きさ、パワー、移動スピードなどから、安全面を考慮して一般的には安全柵の中に設置されることが大半です。
一方、「コボット」(人共生ロボット)は、人と機械が密接に連携する必要がある生産ラインにおける作業を可能としました。コボットは、作業のパワーとスピードを細かく調整できるロボットアームです。とても器用である上に、新しい作業を行う際に簡単にプログラム変更できることが特徴です。
現場のアイデアから生まれるオートメーション「からくり」
「からくり」とは、電気やコンピューターを使うのではなく、テコの原理や重力などを活用した機械的な装置の社内通称です。この通称は皆さんもおなじみ江戸時代の日本の伝統的な機械仕掛けの人形に由来しています。自動車メーカーでは、からくりを使って作業工程に適した部品を自動的に作業者に届けるなど、作業の効率化・簡素化を図っています。日産の工場でも、さまざまなからくりが取り入れられています。
日産の工場でも、社内で作られたさまざまなからくりが取り入れられています。からくりのアイデアを出していくことは、コスト削減と生産性向上を両立すると同時に、単調な作業を省きミスを防ぐための独創的な作業といえます。また現状に満足することなく、常により良い改善を追求し続ける日産の企業文化も垣間見ることができるでしょう。例えば「いるだけちょうだい」は、あらかじめ設定した個数の部品を、手をかざすだけで取り出せるからくり装置で、作業者が部品の数を数えたり、歩いて部品を取りに行ったりする手間を省くことに役立ちます。
作業員の負担を肩代わりする外骨格
日産のバルセロナ工場で試験的に導入されている外骨格(エクソスケルトン)は、作業員の負担を軽減し怪我のリスクを抑えるための装置です。外骨格は軽量(1.5~3kg)で、上の方を向きながら頭より高い位置で作業を行う際に、作業員の肩と腕をサポートし最大で60%の負担を軽減することができます。
これまでの自動車生産の現場では、高度な技能訓練を習得した、たくさんの人に工場で働いてもらう必要がありました。しかし今回紹介した様々な取り組みにより、生産性の向上はもちろん、作業員への負担が軽減することで女性や高齢者が活躍できる職場環境を提供することができます。「未来のクルマは人がつくるもの」という日産の信念に基づき、これからも日産はすべての作業員が働きやすいと感じる職場環境を実現するために挑戦し続けます。
関連リンク「UR-10コボット」
外骨格(エクソスケルトン)実証実験(英語のみ)
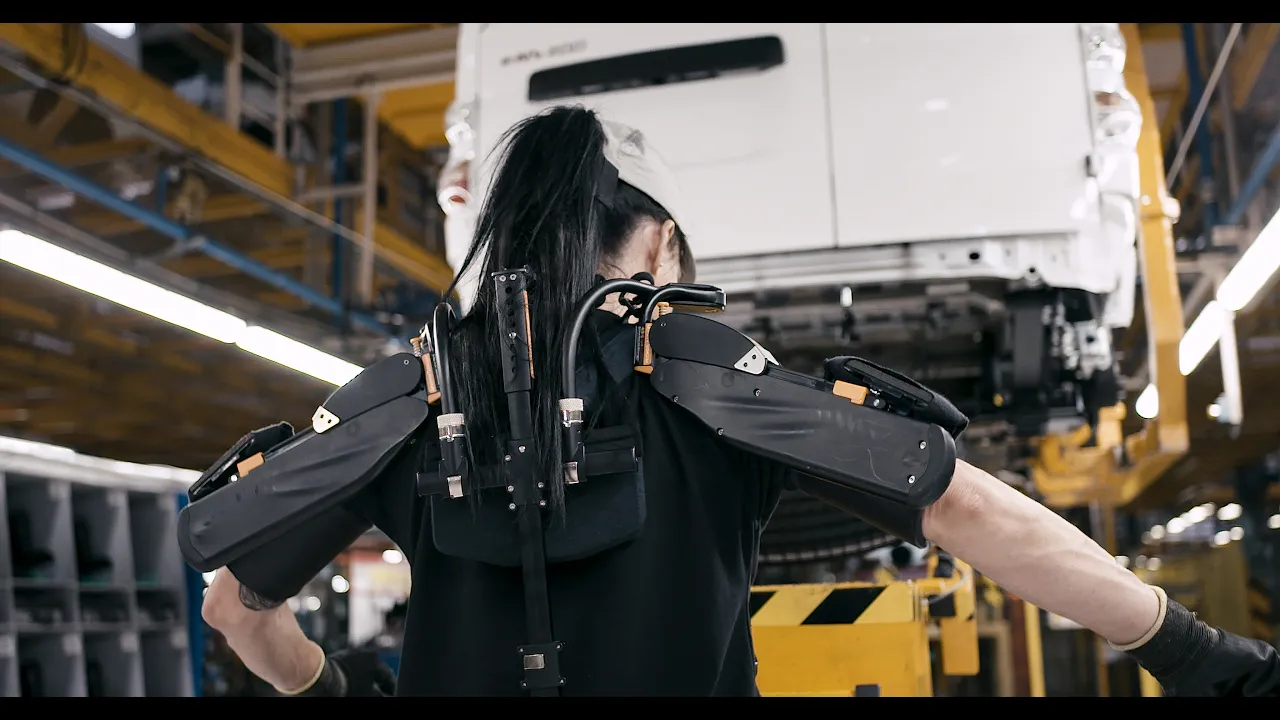