水木しげるの「ゲゲゲの鬼太郎」が出迎える鳥取県の米子空港からほど近い米子市で、日産 栃木工場に勤めて今年で45年目になる技術者の星 広美が生み出した生産現場でのアイデアが開花しようとしています。
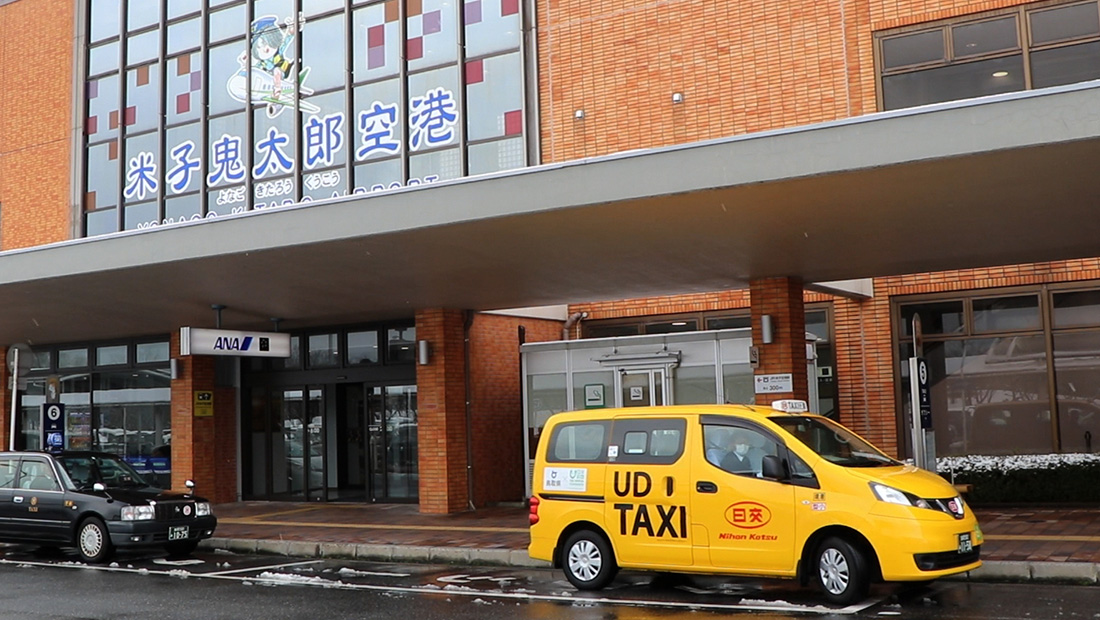
改善は、1秒に満たない単位のロスを防ぐことから
クルマのモノづくりの現場では、より精度の高い効率的な生産ラインの実現に向けて日夜改善活動が行われています。その活動は多岐にわたっており、新たな産業機械の導入やラインの改修などによる、大規模で根本的な改善活動もありますが、星が栃木工場で取り組むのは1秒にも満たないわずかな時間のロス(ロスタイム)を防ぎ、正確性を高めることでした。「コンマ何秒」という次元のロスタイムを防ぐことにどれほどの意味があるかと疑問に思うかもしれませんが、年間何十万台ものクルマを生産する工場の現場においては、その積み重ねが生産時間の節約になり、ひいては生産現場の効率を高めることになるのです。工場ではこのような、日常生活では気にしないようなほんのわずかな時間もムダにしない工夫があらゆる工程に取り入れられており、継続的に改善活動が行われています。
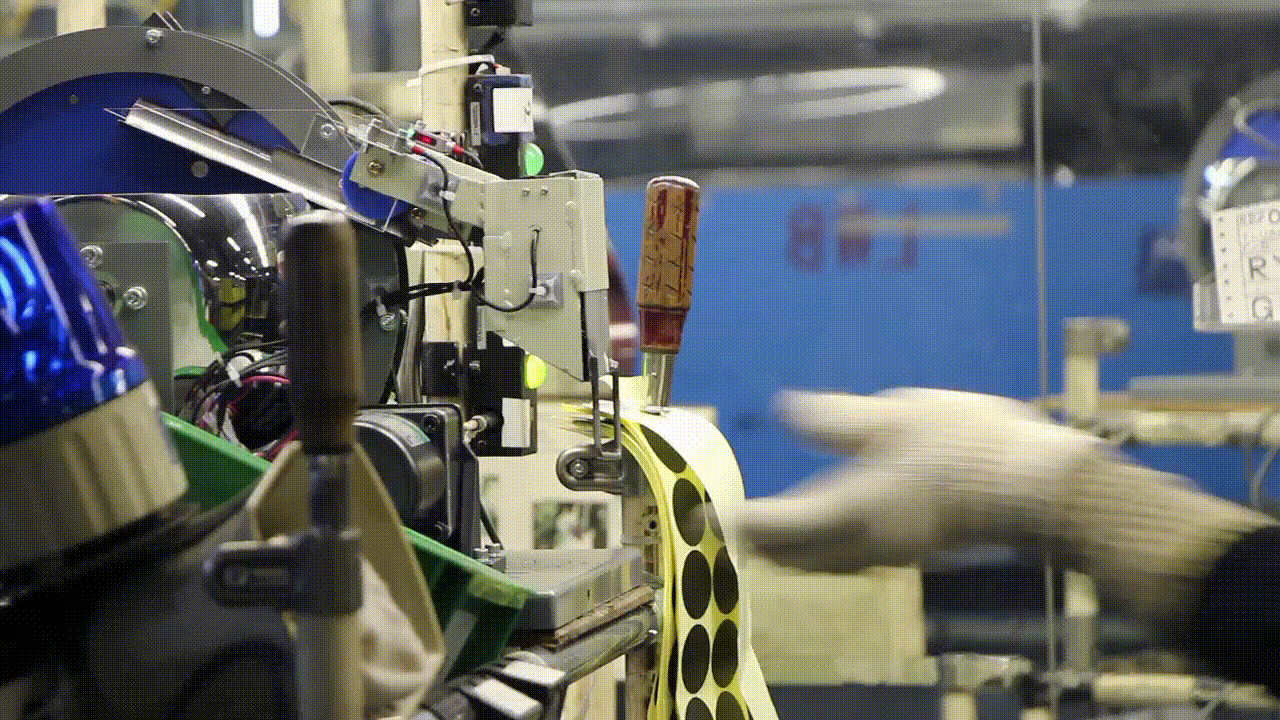
金物屋のボウルから生まれた「パーツフィーダー」
星が開発した「パーツフィーダー」は、ボルト(ねじ)やナットなどクルマの組み立てに必要な部品を決められた数量分自動で供給する装置です。半年がかりで練った構想案のもと、金物屋にあるボウルを使って星自身が溶接を行い生まれました。最終的に生産される商品価格の負担にならないよう、低コストで装置を生み出すことも工夫のひとつであり、身近に入手できるものを活用することは決して珍しいことではありません。さまざまな容器の検討を通じてたどり着いたキッチンで使われるボウルの球体は、同装置の開発にはぴったりだったのです。
パーツフィーダーは、日産の混流生産ならではの課題を解決するために生まれました。混流生産とは、例えば栃木工場では「スカイライン」や「フェアレディZ」、「NISSAN GT-R」をはじめとした、さまざまな車種を1本のラインで生産する方式です。混流生産で組み立てを行う作業者は車種ごとに応じた必要数のパーツを正確に準備する必要があります。流れ作業においては作業者が咄嗟に正確な数の部品をつかむのは難しく、誤った数のパーツを手にしてしまったら、不足分を箱から取り直したり余剰分を戻したりしなければならず、無駄な時間がどんどん蓄積されてしまいます。必要な数の部品を正確に自動で供給する手作りのパーツフィーダーは、現場で大変喜ばれ、そのアイデアは特許を取得しました。

クルマ屋はクルマ屋、特許を通じた出会い
現場の精度を高めるパーツフィーダーは、導入したいという声が工場内の多方面からあがりました。しかし、日産自動車はクルマをつくる会社であり、突然「パーツフィーダー」を量産することはできません。また、一度つくられた装置も、定期的なメンテナンスが必要になるので、星が対応できる栃木工場の限られたラインへの導入に留まりました。どんなに良いアイデアが生まれても、日産のあらゆる生産工程での改善に繋げるには、普及という壁がたちはだかるのです。そこで日産が、パーツフィーダーの普及の壁をこえるために手を組んだのが、鳥取県にある「株式会社日本マイクロシステム」です。同社との出会いの場は「知財(知的財産)ビジネスマッチング」でした。
「知財ビジネス」にはさまざまな側面がありますが、その一つに日本経済活性化の源泉として活用する取り組みがあります。それは、知的財産を所有する企業から、技術力のある中小企業に知財をライセンスし、中小企業のビジネスを成長させる、というものです。中小企業が経営基盤を安定化させるための方策として、自社ブランドの製品開発が挙げられますが、中小企業にとって独自製品開発のリソースを確保することは容易ではありません。そこで実績のある大手企業の知財を中小企業にライセンスすることで、中小企業による製品開発の促進を狙っています。その取り組みを加速させるため、近年では、地方の中小企業と特許を所有する企業とのマッチングイベントが地方自治体主導で盛んに行われています。2016年、鳥取の中小企業を知り尽くした「敏腕仲人」である鳥取県産業振興機構の紹介で出会った日本マイクロシステムが、日産のパーツフィーダーの商品化に名乗りをあげました。
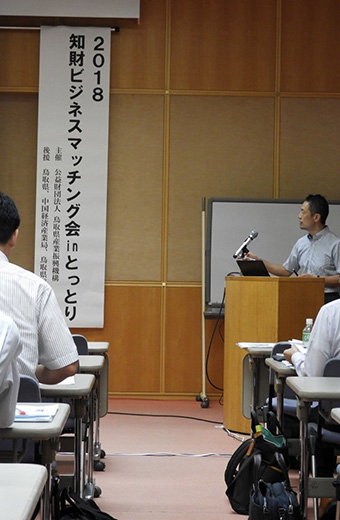
知財は誰かの失敗を重ねたうえでの成果を供与してくれる
日本マイクロシステムは、35年以上前に創業した米子市の地元企業で、ソフトウェアと省力化・自動化機器の開発を行っています。鳥取県産業振興機構は、「これまで企業のカスタムを受けてきた実績と、自動車メーカーに通用するメカトロニクス技術を持っている」ことを見込んで日本マイクロシステムを紹介しました。日本マイクロシステムは「お金を払ってライセンスを取得し、何かをつくるということがイメージできなかった」ものの、カスタムだけでなく自社商品の開発を模索しており、「新しい分野に出るチャンスかもしれないと思った」と当初を振り返ります。そして2016年に日産とライセンス契約を交わしました。
早速、ライセンスされた知財をもとに開発が行われ、半年後には「オービットフィーダー」という樹脂製の締結部品を自動供給するパーツフィーダーが商品化されました。通常、日本マイクロシステムで自社の商品開発にかかる期間は早くても5年はかかると言います。それに比べると、半年という期間は驚異的なスピードです。日本マイクロシステムの松本課長は「失敗を含め、誰かがやって経験を積まれた分を享受しているので、早く仕上がったのだろう」と語ります。完成した樹脂パーツフィーダーは同社にとっては、念願の自社商品でもあります。その後商品は、日産の自動車工場をはじめ、日産に部品を納品するサプライヤーにも導入されました。
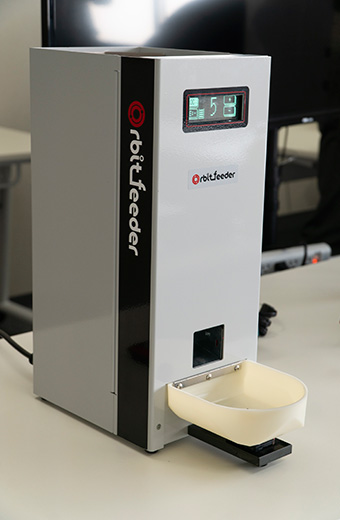
さらなる「自社商品」の開発へ、挑戦は続く
2020年春、星は3回目となる米子市を訪れていました。金属のボルトナットを供給する試作機のワークショップを行うためです。2017年に樹脂パーツフィーダーの販売を開始しましたが、多くの営業先から「ボルトナットの供給装置も作れないか?」という声があがりました。やはり日産同様、多くの製造業においてボルトやナットを正確に取り出す装置のニーズは高いことが判明したのです。そこで日本マイクロシステムは日産からの知財ライセンスのもと、ボルトナットフィーダーの製品化にも取り組むことにしました。ワークショップでは、考案者である星が日本マイクロシステムを訪れて、試作機へのフィードバックを交えてディスカッションを行います。「(商品を)導入したらどうなるか、という部分を考えるのに何年もかかることもある。実際に使用される現場からのフィードバックは大変ありがたい」と日本マイクロシステムの尾見部長は言います。実用性の高い商品の開発には装置としての操作性はもちろん、例えばどのような場所に置かれるのか、メンテナンスの望ましい頻度などといった導入側の細部にわたった視点が欠かせません。
「45年間勤めた成果と証になる」──パーツフィーダーの商品化を目前に、星ははにかんだ表情を浮かべました。日本マイクロシステムの若い技術者たちと白熱したディスカッションを繰り広げる彼は、今年で日産を退職します。「喜んで受け入れてもらえるような商品にしないと、提案した側としては寂しいものがある。だから一生懸命良いものにしたい。どこの業界でも、みな同じような苦労をしているのではないか。この技術をさまざまな場所で活用してもらいたい」と語ります。星と自社技術者の議論を見守る日本マイクロシステムの高島代表取締役は、「設計したものが、自動車工場で今まで改善をしてきた人たちに評価されるのは若手の自信になった。これまで電機業界との取り引きが多く、ほとんど縁のなかった自動車業界と接点が持てたことも大きい」と今後のビジネス展開への期待を語ります。
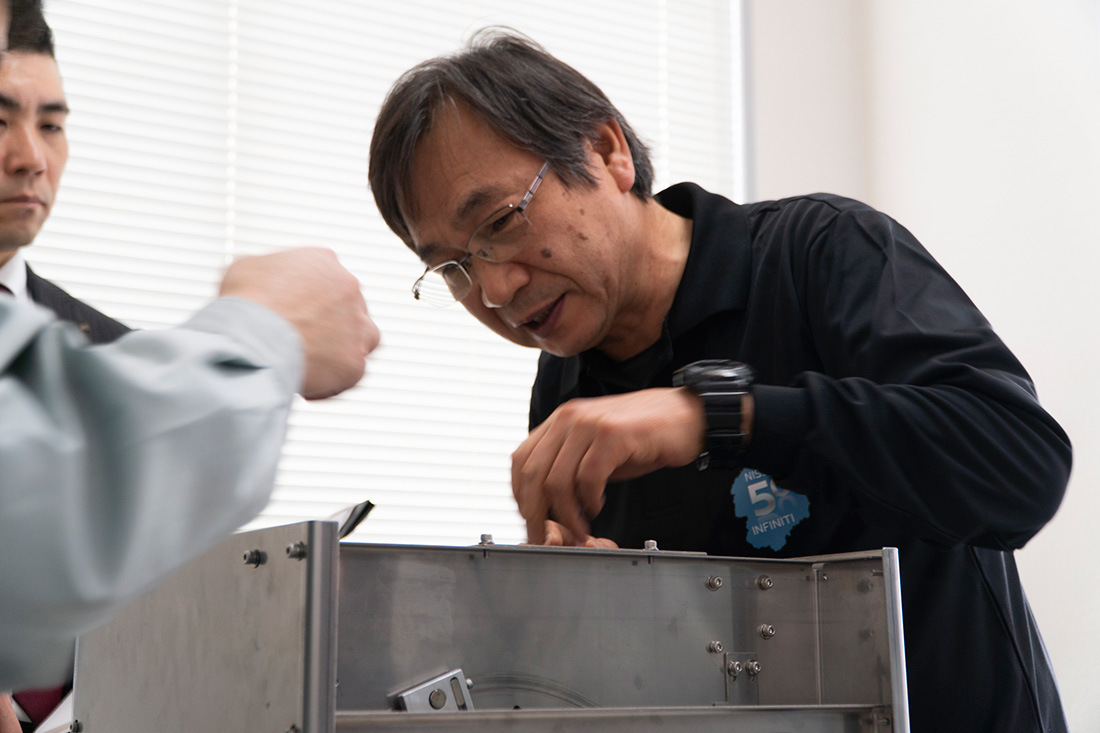
情熱の産物、自社商品としての開花
2020年春のワークショップは、ボルトナットのパーツフィーダーの開発におけるマイルストーンにもなりました。日本マイクロシステムが考案した、独自の機構に特許取得の可能性が見えてきたのです。それは、日本マイクロシステムにとっても、星にとってもうれしい発見となりました。栃木工場での課題解決手段として考案され、ボウルから生み出された装置は特許を介して、遠く離れた鳥取の技術者の手に渡りました。さらなる自社商品の開発により会社を育てようとする若い技術者たちは、熟練の栃木の技術者からノウハウを吸収し、よりよい商品の開発へと邁進しています。ワークショップを終えて星はこう振り返りました。
「自分と同じモノづくりを志す若い技術者たちに、長年培ったノウハウを伝授できることは大変嬉しいことだ。その喜びは、社外の技術者であっても変わるものではない。次世代の技術者たちがこの先の新しいものを創りだしてくれるだろう。」
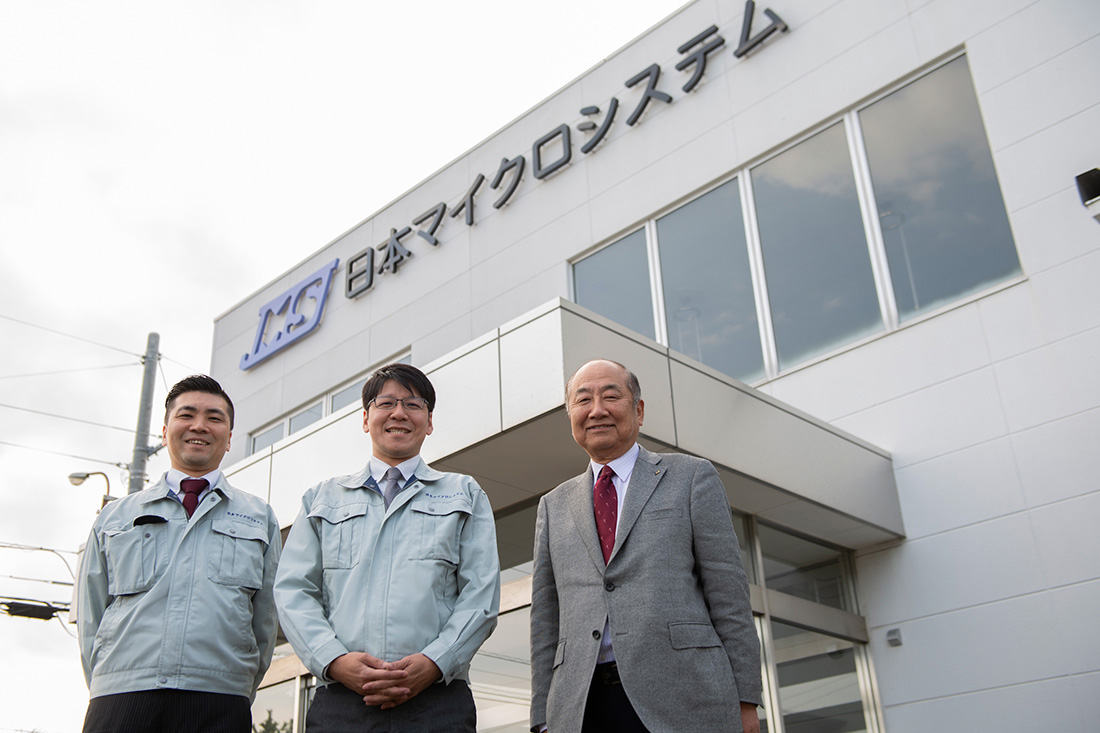
〔左:松本課長 中央:尾見部長 右:高島代表取締役〕
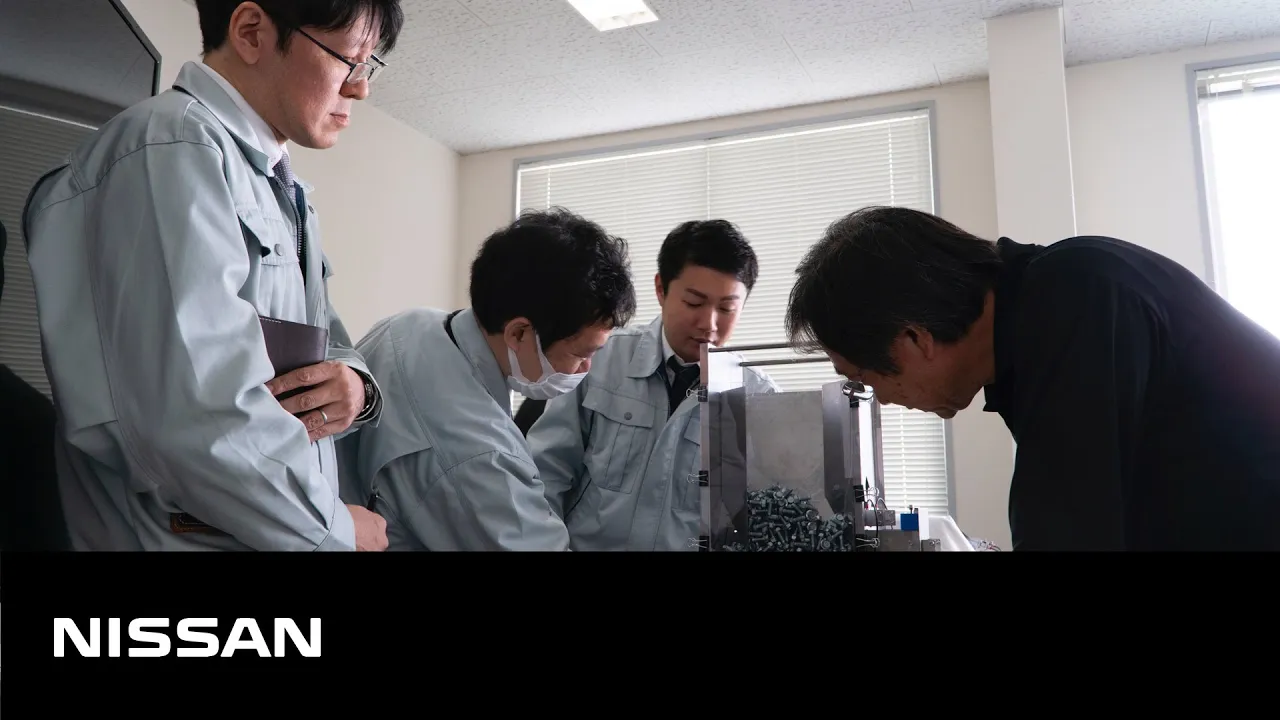