レジェンド 05:生涯を工場に捧ぐ、高橋 忠生。
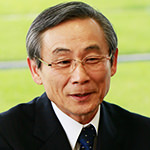
高橋 忠生
1945年、母親の疎開先であった実家の福岡県で生まれる。1968年に東京大学工学部産業機械工学科を卒業し日産自動車(株)へ入社。栃木工場の鋳物工場の立ち上げに携わり1983年にはメキシコ・レルマ工場の工場長に就任する。1992年、同社第一技術部次長として座間工場閉鎖を担当した。1998年に取締役、2002年に副社長、2007年に副会長、2009年に退任し各種外部団体役員を務める。2012年には藍綬褒章を授与された。
海外で工場を作りたい
自動車会社には様々な仕事があり、クルマの設計、生産、販売はもちろんのこと、宣伝やマーケティングや広報などその分野は実に多岐にわたっている。しかし、自動車会社の産業分類は「製造業」。本業はやはり、クルマを作ることにあり、入社以来40年ちかく、それに従事してきたのが高橋忠生である。
高橋は1945年に福岡県で生を受けるが、その後は大学卒業までの大半を東京で過ごす。東京大学工学部産業機械工学科を1968年に卒業。日産自動車へ入社した。
「でも、クルマに対して特に思い入れがあったわけではないんです」
これまで、この伝記で紹介してきたのはいずれもクルマへの強い思い入れがあった人物ばかり。ではどうして高橋は自動車メーカーを選んだのだろう。
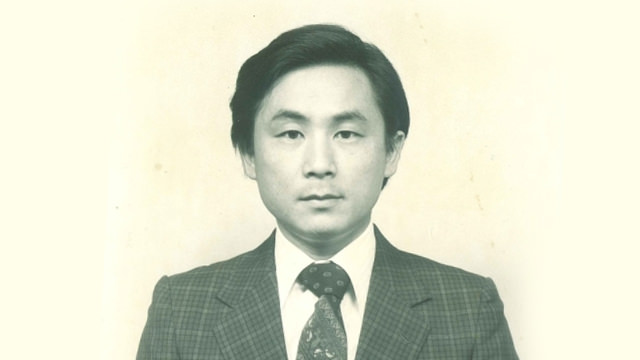
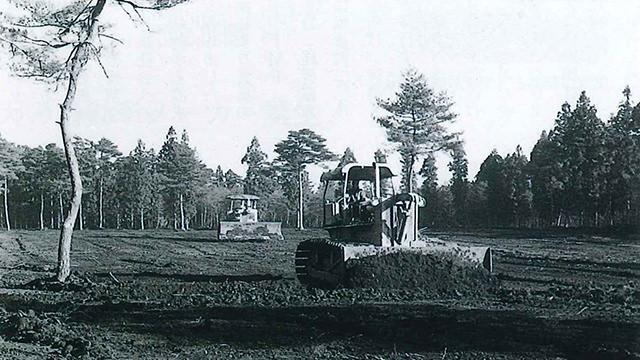
「父は工場技術者でした。小学校2年か3年の時です。父の職場、つまり工場に連れていってくれました。産業用モーターを作る工場だったのですが、窓越しに見たずらりと並ぶ大きなモーターを格好いいなと思った。その映像が記憶に残ったせいでしょうか、特に悩むこともなく工学系に進み、将来は工場に関係する仕事に就きたいと漠然と思っていました。だからクルマ作りじゃなくてもよかったんです(笑)。造船なんかは豪快でいいなと思っていましたし。」
いくつかの入社試験を受け、最終的には日産自動車に決めた高橋は、最初の面接で将来何をやりたいかを聞かれ「海外で工場を作ってみたい」と言う。
「そんなことをいきなり言うなんて、私も若かったのですね(笑)。そうしたら面接官に『そうか、地方でもいいか』と聞かれましてね。大きなこと言ったって、実は工場のことなんかほとんど分からないし、日産の工場がどこにあるのかさえもよく知らなかった。だから質問の意味がよく分からなかったのですが、構いませんと答えました」
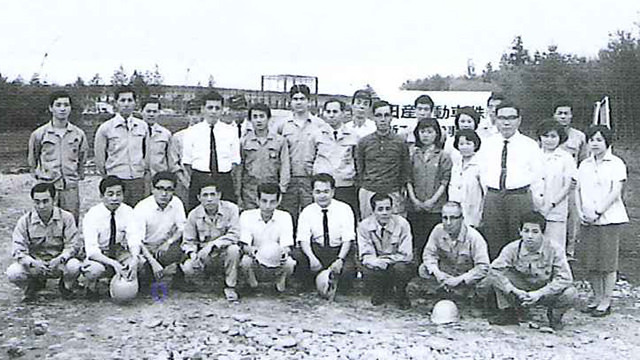
高橋の配属先は上三川(かみのかわ)準備室というところに決まった。そこは、栃木県に建設予定の新工場の準備室で、新入社員の中でそこに配属されたのは高橋ただひとりだった。
「自分で言ったものの、建設の知識なんかまったくないし、ひとりぽっちでしたので不安でしたね」
最初のうちは仕事などできるはずもなく、先輩の後ろをうろうろとついて回るだけの日々だったという。唯一の仕事と言っていい仕事は昼休みにあった。
「昼休みになるとみんなでソフトボールをするんです。敷地が広いから、マイクロバスに乗って移動する。でも私は新入りなので、みんなより先にひとりで行って、ベースを置くなどの準備をしていました。その時ばかりは重宝がられましてね(笑)」
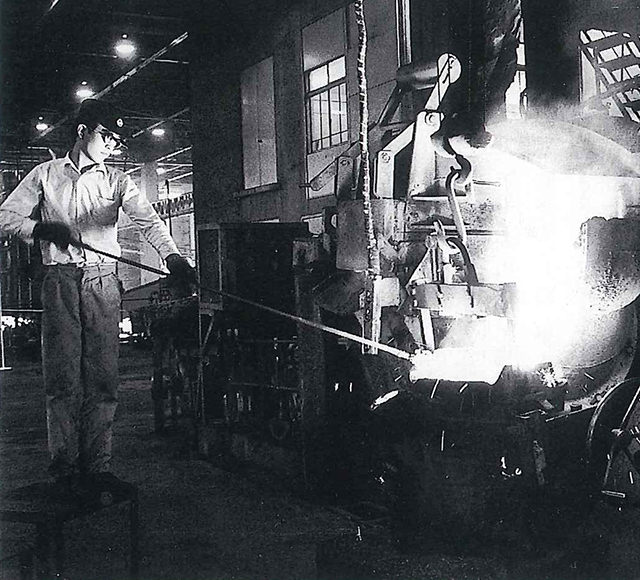
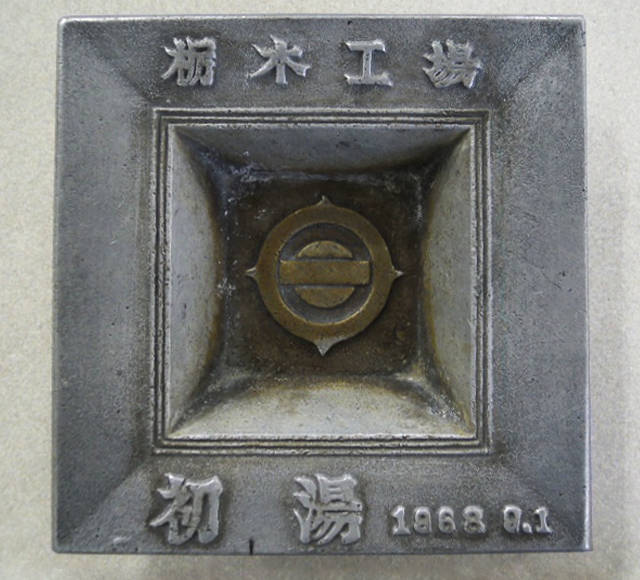
しばらくして、シリンダーヘッドなどを製造するアルミの鋳造工場が完成する。その開所式に関係者に配る「記念品を作れ」というのが、高橋に課せられた初めての仕事だった。
「アルミ鋳物の灰皿をひとりで手作りしました。でも、更地の場所に少しずつ人が集まり建物が出来て機械が搬入され現場の管理体制を整え、そして実際にもの作りが始まるまでのすべての過程を間近で見ることができたのは、大変貴重な経験でしたし、後になってとても役に立ちました」
念願が叶う
高橋は結局12年にわたり、この栃木工場で経験を積んだ。そしてメキシコへの異動を告げられる。1980年のことだった。
「海外工場で働きたいと伝えていたので、実はもう少し早く行けると思っていました。だから、やっと来たな、という感じでした」

メキシコ・レルマ工場はすでに稼働しており、高橋は第2鋳鉄鋳造工場の建設に携わることになる。当初、建設チームの日本人は高橋を含めふたりだけ。他のスタッフはすべて現地人だった。約2年半で竣工まで漕ぎ着け、3年くらいの赴任と聞かされていたからそろそろ帰国かと思っていたところに、「課長に就任だ」との連絡が入る。
「同時に、そのまま工場長として残れと言われました。37歳の時でした。工場にはずっと携わってきましたが、マネジメントの経験はない。同じ工場にいても、それまでの仕事とはまったく違うことをするわけですから、とにかく勉強するしかないと腹をくくりました。だから、うまくいったと自慢できる成果があったかどうか」

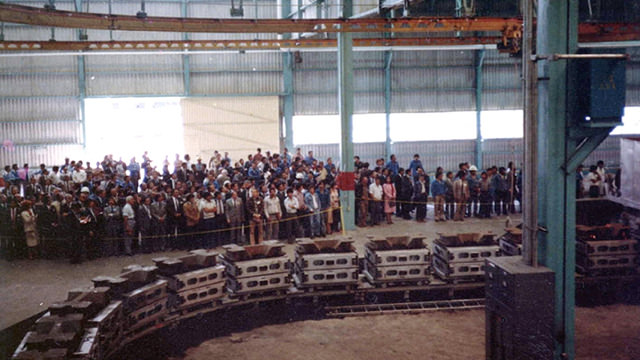
レルマ工場開所式招待状と開所式風景。
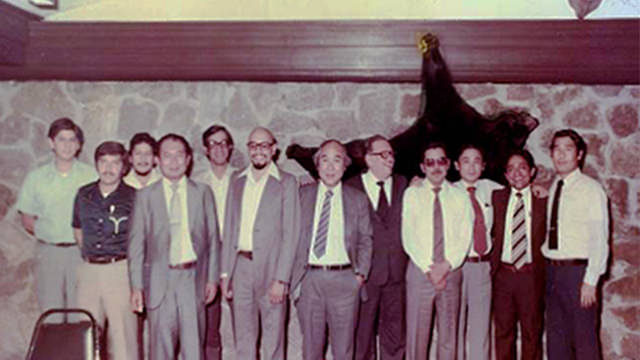
チームよりは「個」の意識が高いメキシコ人をまとめることに試行錯誤しながらも、工場長として3年、トータルで6年間をメキシコで過ごした。帰国して栃木工場の製造課長、横浜工場の工務部次長や鋳造技術部主管を務める。
「ここまでで、入社してからすでに24年が経っていました。ずっと工場で、ほとんど鋳物ばかりを担当してきたことになりますね。やっぱり日本で工場長をやってみたいし、生涯工場でいいと思っていました」
個々の工場の力をひとつに
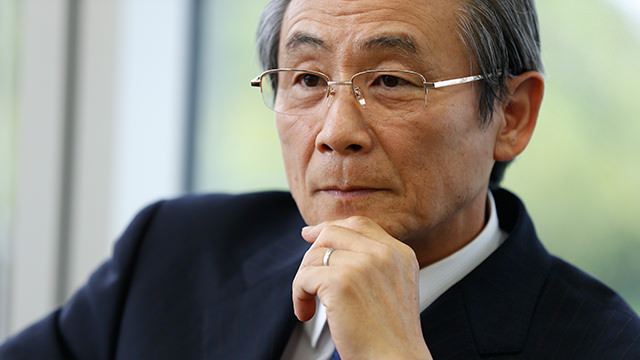
取材に応じる高橋氏
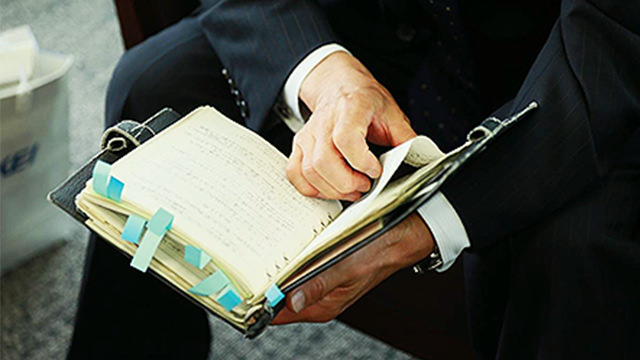
高橋個人の手帳。常に持ち歩き、90年代には同期生産へのアイデアを記していた。
これまでずっと工場を作ってきた高橋が、本社に配属となって最初に担当したことが工場を閉める仕事だったとは、なんとも皮肉な話である。しかしこうした経験が、あらためて日産自動車の生産部門における問題点と見つめ合うきっかけとなる。
「日産にとってはとても厳しい時期で、どうしてそうなってしまったのか、なんとかしないといけない、そんなことを考えるようになりました。そして多くの人の問題意識が盛り上がり1994年、日産生産方式(NPW=Nissan
Production
Way)を作ろうということになりました」
それまでも、生産技術、現場管理、生産管理を個々の工場単位で見ればどこも優秀だったが、全体的な総合力が弱かったという。これらの良いところを集め統一しようというのが日産生産方式のコンセプトだった。
「どの工場も競い合って頑張っていたので、それぞれに特徴を持っていた。でも、みんなの努力が全体の力になるようなシステムに欠けていたのです。そこで、日産の良いところだけでなく、外部の良いところも学び、ひとつのバスケットに入れて作ったのが最初の『日産生産方式』でした。侃侃諤諤の議論の末、共通認識として『日産生産方式』を作り上げただけでも、とても意味があることでした。
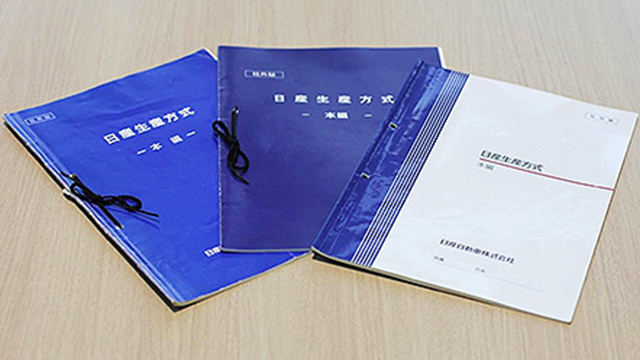

1997年 米スマーナ工場で日・米・英を対象とした同期生産グローバル展開会議を開催。
そして、1997年、海外工場や部品メーカー、物流会社も巻き込んで改革を進めるには、具体的に目指す姿が必要だということで打ち出したのが、『同期生産』です。同期生産を核とする日産生産方式は、1999年のリバイバルプランを端緒とする日産改革の生産部門の柱となりました。」
日産生産方式という言葉が誕生する前に、日産では「ANSWER」と呼ぶ生販(=生産販売)統合管理システムを運用していた。これは、お客様からの注文がディーラーからオンラインで毎日入ってきて、それに合わせた生産計画を立てる仕組み。これは良い仕組みだと高橋は思ったが、あくまで計画作成の仕組みに過ぎなかった。
「ANSWERにより、車両完成日の4日前に、お客さまの受注に基づく、1台ずつの順序と完成時刻の計画が作られていましたが、現実は守りきれていませんでした。それを一台一台、徹底的に順守しようというのが『同期生産』の根幹の考えでした。そこで、『時間遵守率』と『順序遵守率』を同期生産の中心指標としました。時間と順序の計画を日産のラインだけでなく、すべてのサプライヤーや輸送会社に配信し、皆で守っていこう。これが同期生産の始まりでした。
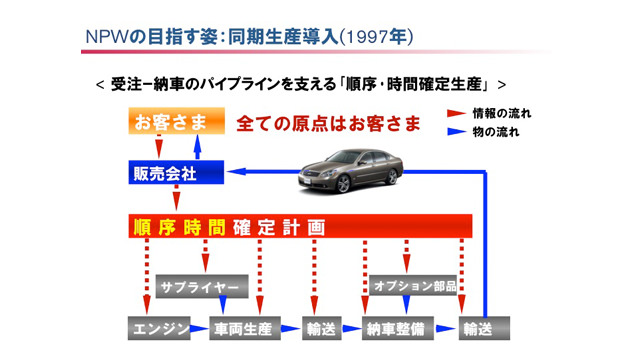
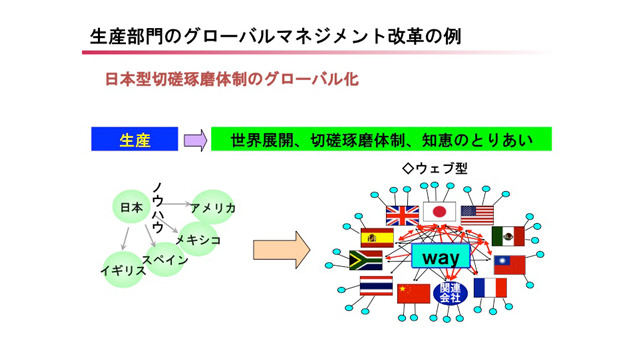
でも最初のうちは大変でした。順守率は2割くらい。日産工場、サプライヤー、物流会社での故障や品質不良や管理ミスなどが順序や時間を乱し、あらゆる課題が『見える化』されました。同期生産のもっとも重要なポイントのひとつがここにあります。世界中あらゆるところであらゆる課題が日常的に『見える化』されることです。見えれば改革が進みます。同期という方向に向かってノウハウが蓄積され、個々の努力が全体の力になるのです。いまではみなさんの努力で、100%近い遵守率を誇る工場が世界に広がっていると聞いています」
NPWのグローバル展開においては、日本中心の展開からウェブ型へとノウハウの伝達方法が進化していった。
メイドバイニッサン
生産技術は日進月歩の進化を遂げ、工場の近代化も急速に進んでいる。順序と時間の遵守や品質の安定のために、将来的には自動車工場も完全自動化になるのだろうか。
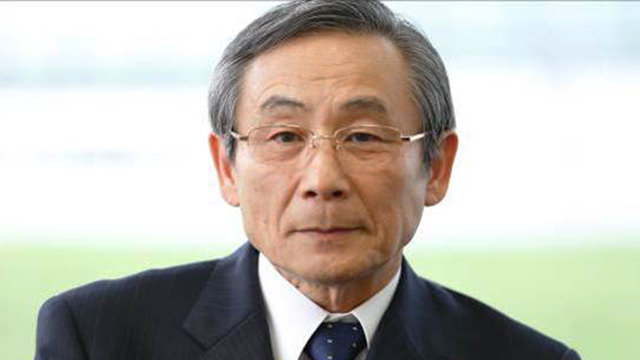
「電気自動車などの構造がさらにシンプルになり自動化技術が進歩すれば、自動化はすすんでいくと思います。が、世界のあらゆる市場の人に評価され、成長を続けるには絶え間ない改善、品質向上が不可欠です。
そして、その原点は、やっぱり現場にいる人間の知恵と力だと思います。生産現場は品質や安全を「守る」ことと、工程や品質の「改善」をすることの両方を実行することが求められます。これはとても大変なことですし、グローバル日産で取り組むべき課題です。優秀な現場の人が増えて、世界中のあらゆる日産の工場が世界に誇れる優れた品質のクルマを低コストで作るようになれば、メイドインどこそこでなく、メイドバイニッサンが常に世界をリードするブランドになるのだと思います。」
巷では「匠が作る逸品」や「熟練職人の手による限定商品」など、少数しか作れない物には価値があるとされ、おしなべて高額な値段が付けられている。それが貴重かつ稀少な製品として珍重されるのは理解できる。一方、大量生産による商品は安価で安易、商品価値も低く見られがちだ。しかし、約3万点もの部品を正しい順序で正確な位置に取り付け、時間通りにまったく同じ品質の製品を月産数万台も完成させる自動車の生産も、決して匠の技術に勝るとも劣らないのではないだろうか。
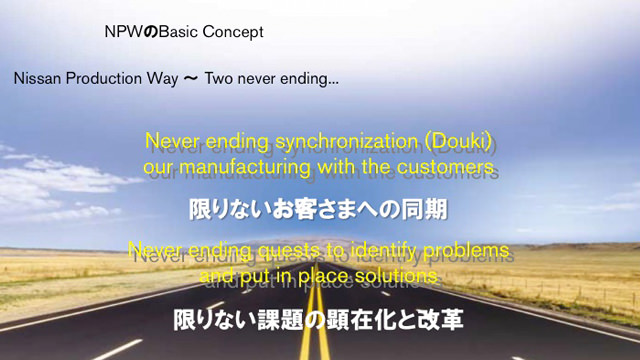
NPWの基本コンセプト、「2つの限りない」
ライタープロフィール
渡辺
慎太郎
/
Shintaro
Watanabe
1966年東京生まれ。アメリカの大学を卒業後、自動車専門誌「ル・ボラン」の編集者を経て1998年にカーグラフィック編集部へ。2003年に退職し、編集プロダクション「(有)MPI」の代表を務めるとともに、自動車ジャーナリストとしても活動を始める。現在はカーグラフィックの編集長も務める。