輸送の効率化
日産は、2000年から自社手配のトラックがサプライヤーを回り、必要な部品を引き取る「引取輸送方式」を、海外を含む多くの生産工場で広く採用し、グローバルに効率化を推進しています。また、サプライヤーと共同で納入頻度の適正化や輸送ルートの最適化、梱包仕様(荷姿)の改善に取り組み、積載率の向上とトラック台数の削減を進めるとともに、トラックから鉄道へのモーダルシフトルートの拡大を積極的に推進しています。
また、完成車やサービス部品の分野で取り組んできたOEMとの共同輸送を、2014年より生産用部品の領域にも拡大することで、さらなる効率的な輸送の実現を目指しています。このほかにも、工場で必要な生産用部品を、できる限り工場近辺から調達することにより、輸送距離を短縮する取り組みも行っています。
点数が多く、多種多様な材質・形状をしている自動車部品の荷姿の工夫にも力を入れています。「物流サイマル活動」として、新車の設計開発段階から輸送効率を考慮した部品設計に取り組み、クルマ1台当たりの部品調達荷量を削減することで、輸送量の削減を目指しています。
またコンテナ輸送については、寸法が大きいコンテナ(40フィートハイキューブコンテナ)を採用し、シミュレーションソフトを使いコンテナ内の無駄なスペースを削減するなど、部品輸送のコンテナ充填率向上を推進しています。
物流手段についても随時見直しを行い、海上輸送および鉄道輸送へのモーダルシフトを推進しています。日本での完成車輸送は、約80%を海上輸送で行っています。関東地区から日産自動車九州株式会社の工場への部品輸送はほぼ全量を鉄道や船舶で行っており、特に船舶へのモーダルシフトについては優良事業者として国土交通省からの認定を取得しています。
海外拠点においては、それぞれの地理的特性を生かした輸送手段を選択しています。輸送先に応じて鉄道や船舶を使い、従来のトラック輸送からの切り替えを推進しています。中国では国内向け完成車輸送に船舶および鉄道を利用する比率を高めています。
太陽光発電パネルなどの省エネ装置を採用した自動車運搬船を導入
日産は、グローバル物流におけるCO2排出量削減に向けて、省エネ型自動車運搬船の導入を推進しており、2017年までに7隻の省エネ船を導入しています。海外では「City of St. Petersburg」「City of Rotterdam」、国内では「日王丸」「日清丸」「日昇丸」「玄武」「デイブレイクス ベル」を導入しました。「日清丸」は、太陽光発電パネル、電子制御ディーゼル船舶エンジン、全艙内及び居住区のLED照明及び最新の低摩擦抵抗塗料など省エネ装置を採用し、従来の同型船舶と比較すると、年間最大約4,200トンのCO2排出量を削減することができます。
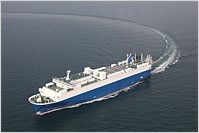
省エネ型自動車運搬船(写真は「日王丸」)