Clean Diesel Technology : Newly developed Diesel Engine M9R
The M9R engine introduced in Europe from 2007, combines all the elements of power, quiet engine, and affordability. This clean diesel engine drastically reduces NOx and PM emission levels.
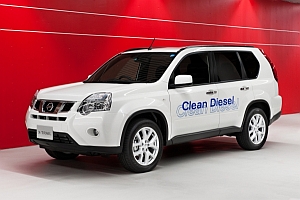
Features
To enable high combustion efficiency, the engine employs the latest 1600 bar common rail system and high-precision piezoelectric-controlled injectors that respond up to four times faster than conventional devices. By positioning the inlet and exhaust ports "in opposition," a double swirl effect is created, which improves distribution of the air/fuel mixture for enhanced combustion efficiency. Furthermore, a periodic-regeneration diesel particulate filter provides the capability to continuously remove particulate matter from the exhaust. the Continuously Variable Valve Timing Control System (CVTC). Emissions are also cleaner, thanks to more rapid catalyst activation.
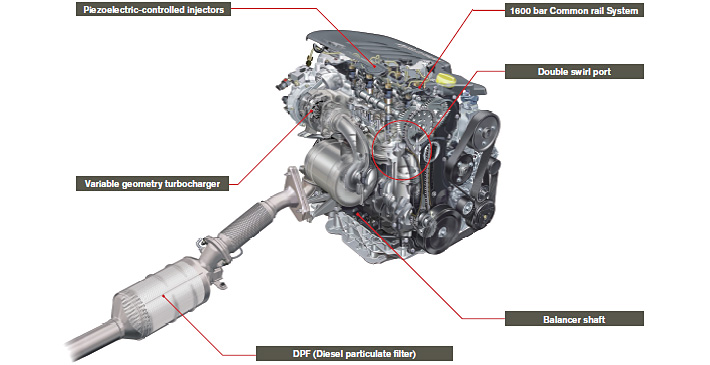
System configuration
Piezoelectric-controlled injectors
Compared to previous solenoid-actuated systems, the inclusion of piezoelectric elements allows faster action and has dramatically improved fuel injection timing and accuracy of injection quantities.
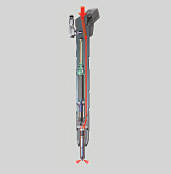
Variable geometry turbocharger
Improvement in power output and torque is realized by optimizing the vane shapes, reducing friction, and improving aerodynamic features.
1600 bar Common rail System
Combustion efficiency was enhanced by raising injection pressures to extra-high levels (1600 bars) and with advanced control of fuel injection using the piezoelectric-controlled injector. At the same time, the incidence of particulate matter is curbed.
Double swirl port
Swirl flows are accelerated by placing the exhaust and intake ports in opposed positions. This allows better efficient mixture of air and fuel, and contributes to superior combustion efficiency.
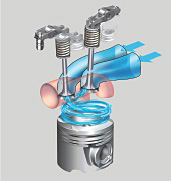
Balancer shaft
By repressing engine vibrations, quietness was improved.
DPF (Diesel particulate filter)
After trap of particulate matter generated by combustion, 1 DPF temperature is kept at approximately 600°C, 2 the particulate matter is oxidized, and 3 the cycle is repeated. Through this, periodic-regeneration of DPF is conducted, making it possible to clean exhaust gas repeatedly.
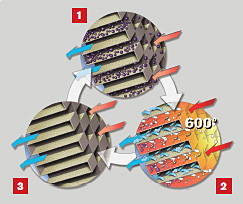