e-POWER's internal combustion engine achieves 50% thermal efficiency
Efficient, fixed-point operation is achieved by restricting the engine's operating range, which is only possible for an engine that is dedicated to electricity generation
Improving engine efficiency is an issue that is common to automobile manufacturers, and a maximum of approx. 42% thermal efficiency*1 is being achieved. However, it took almost 30 years to improve thermal efficiency from 30% to 40%.
With e-POWER, Nissan specializes the role of the engine for electricity generation, and, furthermore, achieves a thermal efficiency of 50% through lean combustion*2 based on the unique STARC*3 concept and waste heat recovery technology.
This makes it possible to further improve fuel efficiency and to reduce CO2.
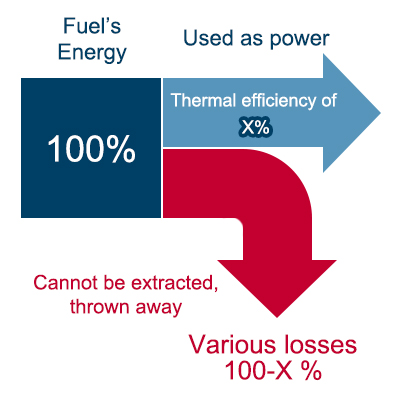
- Thermal Efficiency: Ratio of the fuel's energy that can be extracted as power
- Lean Combustion: Combustion with an air-fuel mixture ratio that has more air than the theoretical air-fuel ratio (wherein the fuel and oxygen reaction have perfect proportions; that is, the ratio of completely burned air to fuel). Lean combustion with an excess air ratio of λ = 2 is assumed.
- STARC: Strong Tumble & Appropriately stretched Robust ignition Channel
System Mechanism
By specializing the engine for electricity generation, it can be operated in its most efficient range. Furthermore, Nissan will continue to develop its battery technology to achieve fixed-point driving to achieve the most efficient driving possible. Through this, fuel economy can be improved.
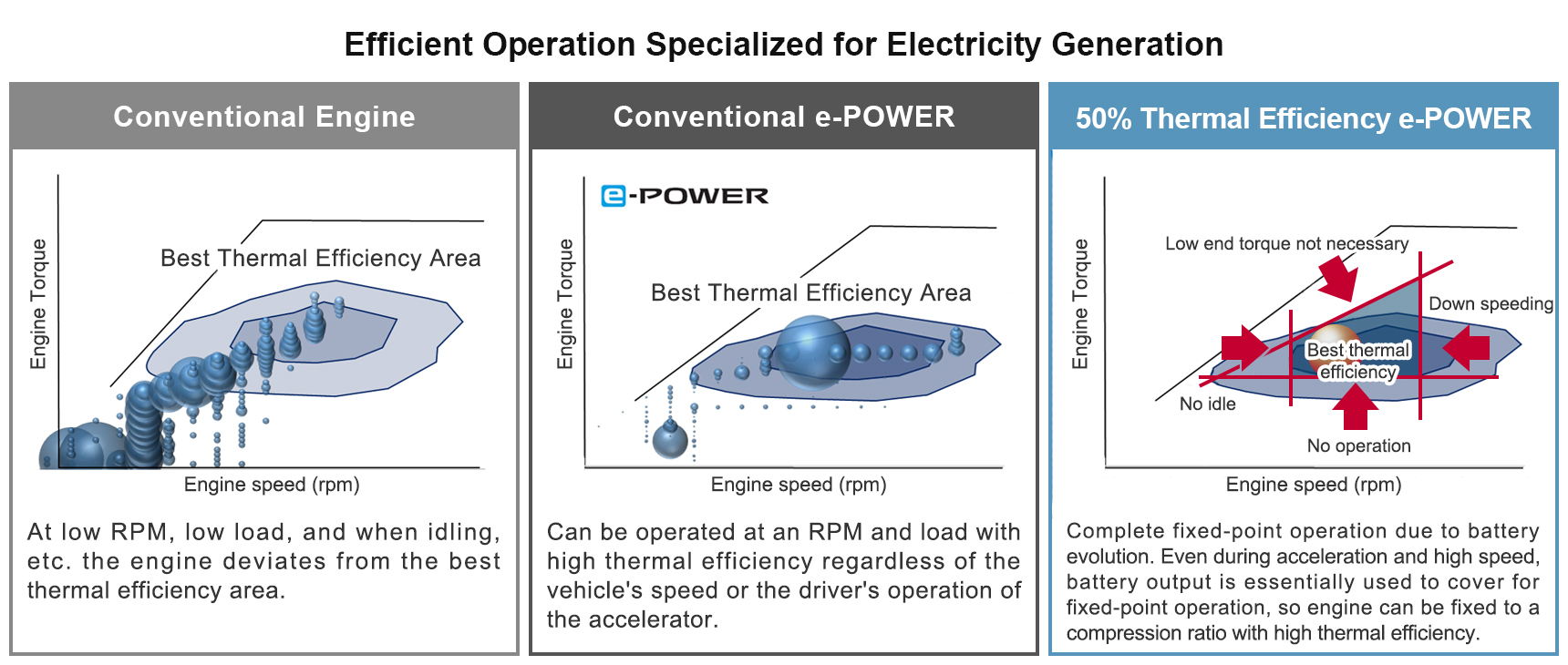
Based on the unique STARC concept, the intake manifold, combustion chamber, and piston shape are optimized for the fixed-point operating range of the electricity generation engine and form a stable and extended spark plug discharge channel*4 by maintaining a strong tumble flow in the center of the cylinder. This enables stable combustion under highly diluted conditions, such as high EGR*5 and lean combustion, and improves thermal efficiency.
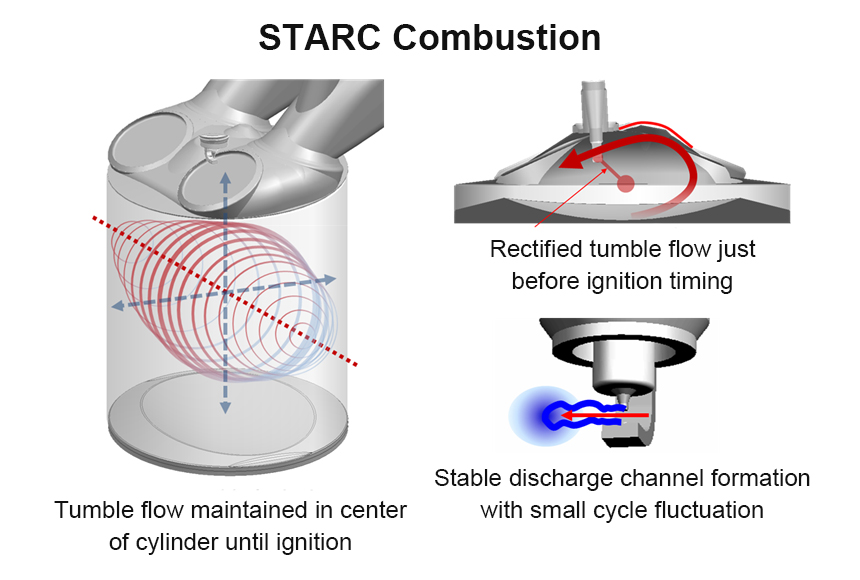
- Discharge Channel: The flow of electricity through the air discharged for ignition.
- EGR (Exhaust Gas Recirculation): Technology that recirculates a portion of the exhaust gases after combustion, intaking them again. Although combustion of the air-fuel mixture diluted via EGR improves thermal efficiency, ensuring combustion is a challenge.
Measures to Achieve 50% Thermal Efficiency
For conventional engine technologies, basic thermal efficiency was improved by lengthening the stroke and reducing friction.
Furthermore, by restricting the engine's operating range utilize e-POWER, it is possible to improve the theoretical thermal efficiency using high EGR combustion under the STARC concept, reducing intake and exhaust losses via the dedicated turbo, achieving a net thermal efficiency of 42%.
Additionally, due to the evolution of battery technologies in the future, through the shift to fixed-point operation, the engine will achieve 50% thermal efficiency through lean combustion based on the STARC concept, even further reductions in friction, and efficient recovery of waste heat.
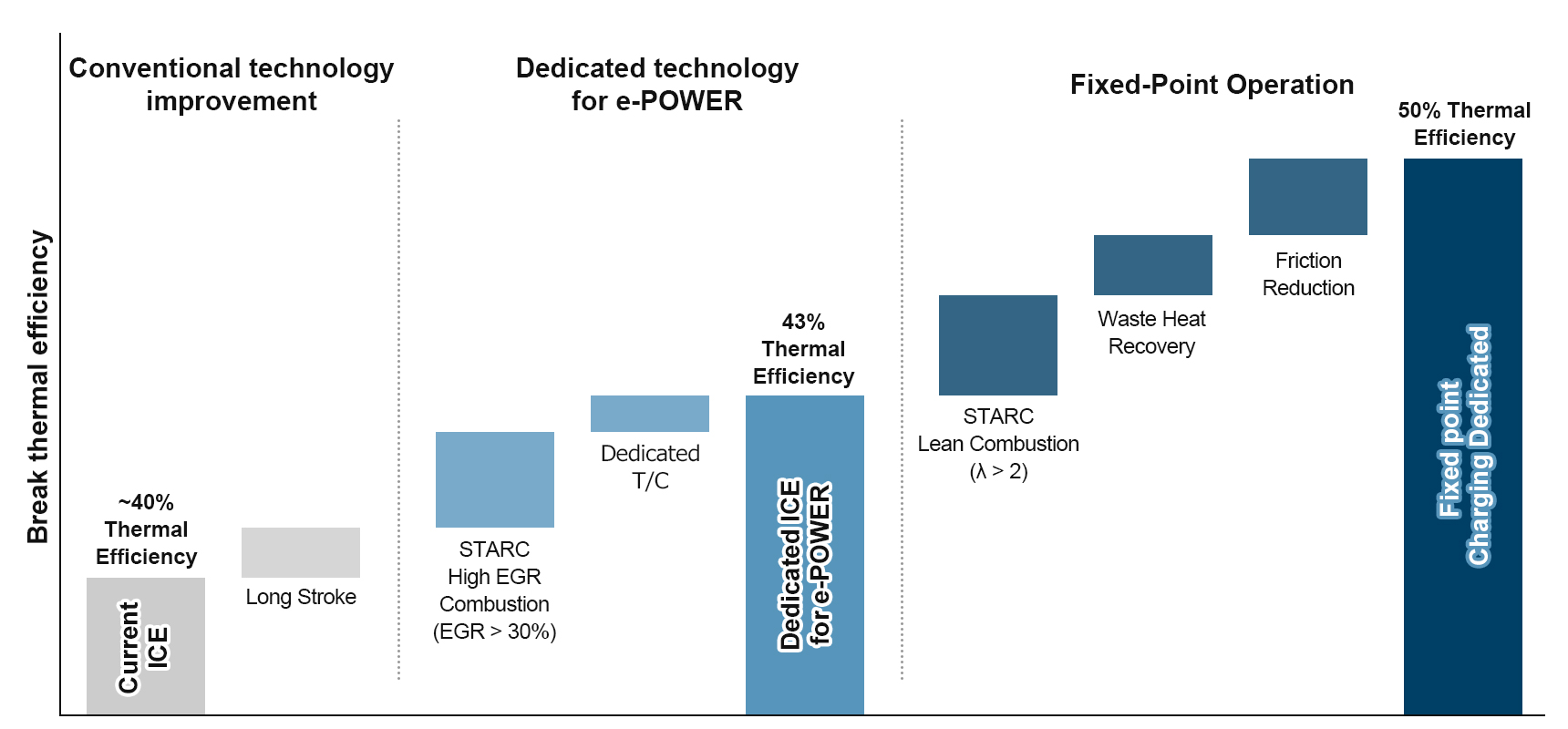