クルマでの取り組み
環境に負荷を与える物質の使用を避け、リサイクルのしやすさを考慮した設計を行います。
また、枯渇性資源の使用量を削減するために、再生プラスチックなどのリサイクル材や、植物由来の再生可能な資源を利用した素材などの利用を進めています。さらに、品質の面から技術的に困難だった使用済み自動車から樹脂部品を回収し、新車部品に適用する仕組みの構築も検討しています。
3R※設計への取り組み
- 設計・省資源化
使用済自動車のリサイクルや部品の再利用を促進し資源を有効に活用していくためには、新型車開発時で3Rを考慮した設計を行うことが重要です。そこで日産では、3Rを考慮した設計を行うための改善要望や新規アイディア等の提案を示す「設計ガイドライン」を作成して、3R設計を進めています。
- リデュースReduce(発生抑制)、リユースReuse(再使用)、リサイクルRecycle(再生利用)。
3R設計のためのプロセス
- 設計・省資源化
日産の商品・開発プロセス業務は、1998年度よりISO14001認証を取得しています。
日産はこの開発プロセスに、新型車開発の目標値として、リサイクル可能率(リサイクルのしやすさ)、解体性効率(使用済み段階での解体のしやすさ)、廃車を原料とする材料リサイクルとその技術の開発、環境負荷物質の削減を設定し、設計段階における判断基準を明確にし、目標値達成状況の評価・管理を行っています。
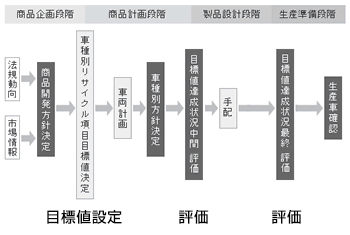
化学物質管理
- 設計・省資源化
材料における環境負荷物質については、欧州ELV指令(使用済み自動車に関する指令)や、2007年6月から欧州で施行された化学品に関するREACH規制*1など、各国で環境負荷物質の使用制限強化が求められています。また日本自動車工業会は、車室内で発生する可能性があるホルムアルデヒドやトルエンなどのVOC(揮発性有機化合物)を最小化するために、2007年4月以降に日本国内で生産・販売する新型乗用車から、厚生労働省が定めた指定13物質に対して指針値を満たすことを自主目標に掲げています。
日産は、2007年に環境負荷物質削減についてグローバルに統一した方針を制定し、環境負荷物質の管理強化、計画的な削減、および代替を推進しており、科学的にハザード(危害要因)が認定された、またはそのリスクが高いと考えられる物質、さらにNGOとの連携により危険性の指摘を受けた物質などを自主的に取り上げ、各国の法規を超える水準まで使用を制限しています。この方針に基づき日産技術標準規格「特定物質の使用に関する制限」において、使用を禁止または管理する化学物質が規定され、開発初期段階から日産車に使用される原材料、部品、用品にまで適用されています。例えば、2007年7月以降にグローバル市場に投入した新型車*2から、重金属化合物4物質(水銀、鉛、カドミウム、六価クロム)および特定臭素系難燃剤PBDE*3類の使用を禁止もしくは制限しています。
ルノーとの提携のもとに、法令遵守のレベルを超えてハザード(危害要因)やリスクの選定基準を見直した共通規格化を実施し、アライアンスでの取り組みを強化しています。日産はサプライヤーとともに、社内とサプライチェーンで情報伝達と管理の仕組みを構築して運営しています。例えば欧州で生産・輸入するクルマや部品については、REACH規制の適合のため情報提供や官庁への登録・届出を行い、CLP規制*4にも対応しています。
- Registration, Evaluation, Authorization and Restriction of Chemicals
- OEM車を除く
- ポリブロモジフェニールエーテル
- Classification, Labelling and Packaging of Substances and Mixture
希少資源の削減
- 設計・省資源化
電動化に必要な部品にはレアアースと呼ばれる希少資源が使用されています。レアアースは資源の偏在や需給バランスによる価格変動が懸念されており、その使用量削減が課題となっています。
日産は2012年にジスプロシウム*(元素記号:Dy)を従来比で40%削減したEV⽤モーターを開発して「日産リーフ」に採用しました。
その後も電動車両の駆動用モーターにおけるDyを継続的に削減し、2020年には「ノートe-POWER」で2010年比85%削減した磁石を採用しました。
さらには2022年「日産アリア」では、永久磁石を使わず、Dyを使用しないEV用モーターも採用しています。
- ジスプロシウム(Dy):貴重な鉱物資源であるレアアース(希土類)の一種。EVのモーター用磁石などに使う。
<省ジスプロシウム技術(粒界拡散技術)>
2012年、日産はレアアースマグネットのサプライヤーと協働し、レアアースのひとつであるジスプロシウム(元素記号:Dy)を従来比で40%削減したEV用モーターを開発、11月にマイナーチェンジした「日産リーフ」に採用しました。EVなどの電動車両用モーターには、その小型化および高性能化に必要な高い磁力を発揮できるNd-Fe-B磁石(以下、ネオジム磁石)を使用しており、ジスプロシウムはネオジム磁石の耐熱性を高めるために添加されています。
これまでは、ネオジム磁石全体にジスプロシウムが均一に分布されるよう添加していました。今回開発したモーターでは、粒界拡散技術を採用し、従来と同等の耐熱性を確保しながらジスプロシウムの使用量を40%削減することが可能となりました。ネオジム磁石の耐熱性を高めるためには、磁石の結晶粒界(結晶の境目)にジスプロシウムを分布させることが効果的であり、粒界拡散とはその特性に着目した技術です。
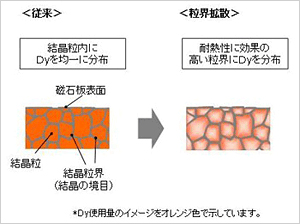
クローズド・ループリサイクルの仕組みを拡大
- リサイクル
クローズド・ループリサイクルとは、生産時に発生した廃棄物、スクラップや、回収した自社の使用済み製品を、同等のクオリティを維持した材料として再生し、再び自社製品の部品に採用する手法です。この手法により、同じ材料を繰り返し使用できるようになり、製品ライフサイクルにおけるCO2排出と環境負荷を大幅に低減させることができます。
特に日産では、クルマの材料として占める割合が高く、かつ天然資源採掘時の環境への影響が大きく、材料製造時や廃棄時に多くのエネルギーを要する鉄、アルミニウム、樹脂という3つの材料のクローズド・ループリサイクルに注力しています。
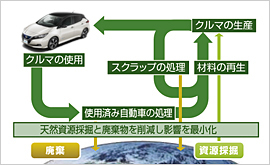
クローズド・ループリサイクル
<鉄・アルミ>
- リサイクル
生産時に発生する端材を減らす工夫に加え、発生した端材をビジネスパートナーと協力しながら回収し、自動車用の材料に再生することに努めています。
使用済み自動車のアルミロードホイールの回収・再生利用を推進しています。
具体的な取り組み:アルミロードホイールの再生利用
日産は、使用済み自動車から回収したアルミロードホイールを、日産の工場内で材料として再生し、高品質のサスペンション部品等へ採用することを可能にしました。これによりバージン材料の使用を削減しています。従来から、廃アルミニウム材はエンジンをはじめとして、幅広くアルミニウム部品としてリサイクルされていましたが、全国のリサイクル事業者で日産のアルミロードホイールのみの分別回収を徹底して行うことにより、より高いグレードのアルミニウム部品に再生利用しています。
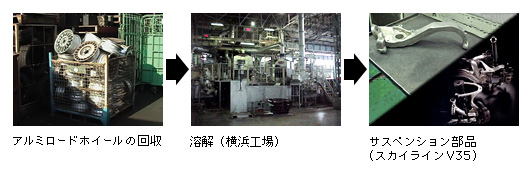
<樹脂>
- リサイクル
工場で発生する塗装済みバンパーのスクラップを、追浜工場の塗装済みバンパー再生工程で塗膜を除去して再生しています。これらは新車用のバンパーに生まれ変わり、「日産リーフ」をはじめ、多くの新車に使われています。
販売会社で交換されたバンパーを再生資源として回収し、アンダーカバーなどの部品の材料として採用しています。
具体的な取り組み:バンパーの再生利用
日産が回収したバンパーを粉砕し、薬品を使用せず従来より安価に塗膜を剥離する装置を開発しました。こうして再び材料とし、補修用バンパー、新車用バンパーへの使用を順次進めています。
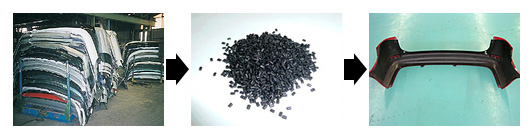
さらにリサイクルの対象範囲を拡大するとともにリサイクル技術高度化による新規天然資源削減をめざし、新たなリサイクル技術の開発に積極的に取り組んでいます。
新たなリサイクル技術への取り組み
- リサイクル
ニッサングリーンプログラムにおける長期ビジョンで掲げている新規天然資源使用量削減に向けて、リサイクル技術もより一層の高度化と対象範囲の拡大が求められます。また、これらの取り組みは日産自動車のみならず、社会全体として必要になるものと考えています。
日産自動車は①シュレッダーダストのリサイクル技術、②軽量車体のリサイクル技術、③電動ユニットのリサイクル技術に重点を置き、リサイクル高度化事業を実施しています。 (最新の実績)
①シュレッダーダストのリサイクル技術
使用済み自動車を再生処理する際に、1台あたり約200㎏前後のシュレッダーダストが発生しています。シュレッダーダスト中の約30%は混合プラスチックであり、現在マテリアルリサイクルされているものは、ASR中の約0.5%にすぎません。自動車のシュレッダーダスト(ASR)削減のため、シュレッダーダストに含まれる混合プラスチックの高度選別を行い、それらの特性に合わせてマテリアルリサイクル及びケミカルリサイクルを行い、自動車用材料として再生利用する技術開発を進めています。
事例) ASR回収樹脂からのリサイクルプロセス最適化
ASR回収混合プラスチックから、自動車で最も多く使用されるポリプロピレン(PP)樹脂を目的とする製品性能に合わせて高度選別し、リサイクルPPとして製造するプロセスの実証をヴェオリア・ジェネッツ(株)及び関係各社と合同で行いました。そこで得られた結果をもとに自動車部品への早期の適用をめざし開発を進めています。
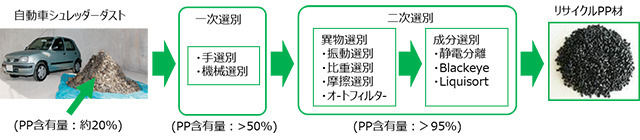
②軽量車体のリサイクル技術開発
自動車走行時のCO2削減を目的に、今後、車体の軽量化のためアルミニウムパネルやCFRPといった軽量素材の採用が増加する見込みです。これらの軽量素材は高い性能、機能を持ち、使用済み自動車としてリサイクルを行う場合、材料価値を維持したままクローズド・ループリサイクルすることが望まれます。
事例)自動車アルミパネル高度選別技術開発
アルミニウムパネルは適用部位ごとの要求特性に基づき、複数の合金グレードが使い分けられています。使⽤済み⾃動⾞からアルミニウムパネルを回収し、再度アルミニウムパネルとしてクローズド・ループリサイクルする為には、合金グレードごとの選別が必須となります。
合金成分の高度選別技術としてLIBS(レーザー誘起ブレークダウン分光法)が注目されていますが、自動車の車体パネルのように全面に塗装された金属材料は、塗装の影響によりレーザーが母材金属に照射されるのを妨げ、選別精度があがらないという課題がありました。日産自動車は(株)マテックと共同でLIBSによる高度選別に適したシュレッダー方法の最適化により、塗装されたアルミニウムパネルスクラップの高度選別プロセスの構築に取り組んでいます。
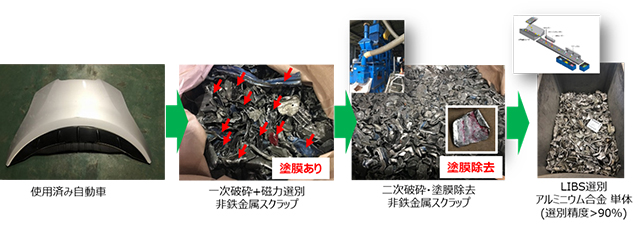
③電動ユニットのリサイクル技術開発
自動車走行時のCO2排出量削減を目的に、ハイブリッド車、電気自動車(EV)が拡大していきます。これらの車両に使用される、リチウムイオンバッテリー、モーターにはレアアースなど多くの希少資源が使用されており、CO2削減と新規天然資源の使用量削減を両立させるためには、その再生利用を進めることが重要です。
事例)駆動用モーター磁石からのレアアース回収技術開発
電気自動車(EV)の駆動用モーターには、希少資源であるレアアースを多く含むネオジム磁石が使われており、レアアース使用量を削減することに加えて、使用済みモーターからのレアアース回収が重要になります。日産自動車は早稲田大学と共同で、高効率なレアアースリサイクル技術の確立を目指し、フラックスとしてNa2B4O7を⽤いた乾式リサイクル法によるレアアースの回収技術の開発に取り組んでいます。
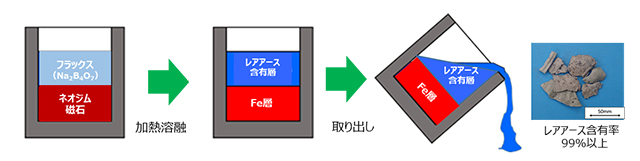