Red Card
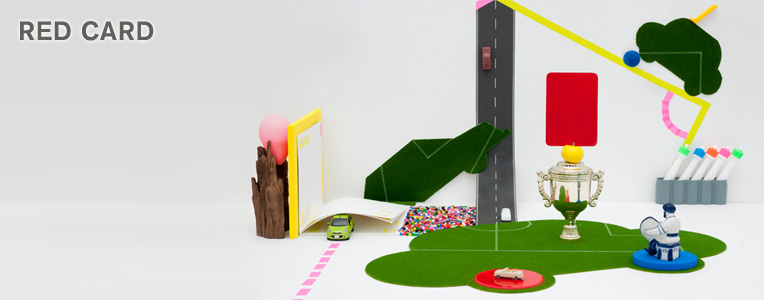
AVES, Nissan' worldwide quality evaluation system, ensures that every vehicle meets the same exacting standards.
Soccer: the sport that makes the world cheer. On the pitch, 23 players. Eleven on each team, and the all important referee.
The rules of soccer are shared the world over, and the referee refers to the 17 articles in the competition rules, which lay out specifications for the pitch and the ball, scoring methods and more, all of which are explained in a 50-page manual. It's only thanks to these shared rules that global-scale tournaments can be held without dissolving into confusion.
Just like soccer regulations, there are rules at Nissan for making cars. This global standard is called the Alliance Vehicle Evaluation Standard (AVES). There are currently 350 AVES check items, and 350 auditors keeping watch over Nissan automobile quality at production centers in 27 countries worldwide.
Before AVES was introduced, car manufacturing at Nissan was a world of artisans. There were no clear stipulated rules, and cars were simply made with the talent of the craftspeople, and sent out into the world.
But gradually production numbers grew, and the number of employees grew, too. To become a global company, Nissan had to be able to manufacture a high quality car in large quantities, and at production bases all over the world.
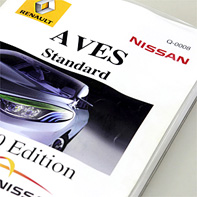
This thick file is the vehicle quality evaluation manual. There are approximately 350 static and dynamic criteria listed.
AVES WAS IMPLEMENTED, TO DEFINE A CLEAR COMMON LANGUAGE, AND STANDARDIZE NISSAN QUALITY.
So AVES was implemented, to define a clear common language, and standardize Nissan quality in the eyes of the customer.
The foundations for AVES were laid out in 1981. In 1988, the items were separated into static and dynamic categories. And on the alliance with Renault in 1999, it reached the form it takes today.
The first checks come in the prototype stage, and are carried out a total of four times before the vehicle is ready to ship. Two certified auditors assess absolutely everything, from the viewpoint of the customer. During the driving evaluation they scrupulously split the work between the driver's seat and the back seat.
And if a car doesn't clear AVES, even if all the preparations have been put into place to begin selling it, the new model can't be shipped.
It is this powerful authority to show a red card that ensures the highest quality across all Nissan's vehicles.
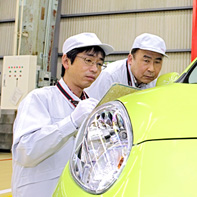
Two auditors conduct vehicle quality evaluation. Naturally they check the exterior and interior, but not even the undercarriage is exempt from their sharp gaze.