Conducting the Orchestra
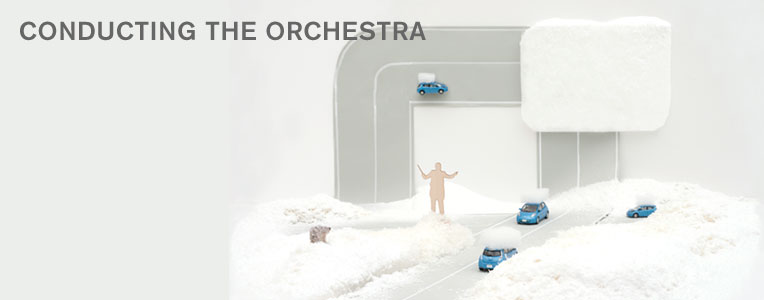
It takes a champion of quality to control all the music.
The conductor steps up to the podium. He picks up his baton. Looking down, he surveys the unenviable task before him. A vast array of musicians, from oboes to violins, kettle drums, harps, even a triangle. He must control them all, keeping everyone in time precisely to the notes on his music sheets, ensuring that each and every bar of sound is always perfect.
And yet he’s not just there for the sake of it. It is only with such a massive orchestra that you can produce the most soaring and beautiful of symphonies.
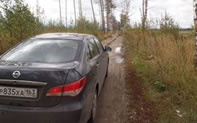
This conductor is one of Nissan’s Overseas Project Quality Directors (OPQD), insuring all the departments involved with making a car give their best performance. The buck stops with the OPQD and there are only around ten of them in the whole corporation. They are the champions of quality.
Just like an orchestra has a range of sections and sounds, so too are Nissan’s operations are cross-functional, involving suppliers, design, testing, manufacturing and marketing – all kinds of different engineering elements over multiple countries and regions, working together as part of an integrated international network.

Russian drivers want a vehicle that can withstand the tough climate and tough road conditions, including heavy snow, rough surfaces, bumps, potholes, high curbs, and even railway tracks.
The conductor must consider not only the roles of each musician in the orchestra pit, but also his audience. If the melody does not sound right to them, they won’t stay in their seats for long. Every note must be played pitch perfect.
The OPQD, much like world-class professional conductors, also go on “concert tours” to other regions to work on harmonizing all local musicians.
Stewart Taylor is an OPQD for Nissan Europe and has been involved with various aspects of quality management in the automotive industry for over sixteen years. His recent “tours” have been taking him to Russia, a market that is experiencing unprecedented growth. But with this development comes new challenges. Firstly, how to ensure all of the parts and vehicles manufactured in Russia meet Nissan’s strict requirements? And secondly, how to provide quality satisfaction to local Russian drivers when their environment and needs are so particular?

Cars washes in Russia are stronger than other regions. OPQD checks that the intense cleaning processes do not damage vehicles and that cars remain watertight.
The OPQD has to identify all the risks where the “music” might be played wrong. Then he or she has to harness all the local instrumentalists to rehearse and get it note-perfect.
The conductors organize “rehearsals” such as the Pre-Start of Sales Quality Clinics (PSQC) to confirm the orchestra is ready to play to the public. For example, in Russia they used local drivers to perform a 20,000km road durability test drive on public roads and in the same scenarios the Russian customer would ultimately experience, all before a single vehicle was even sold.
Let’s consider the climate. Russian drivers need a car that can operate at temperatures ranging from below -30 degrees Celsius to in excess of over 40 degrees. And the conditions in which they drive in over the course of a single day can also vary incredibly, from congested roads in the city to unsurfaced roads near their home in the suburbs.
This being Russia, obviously the car needs to also be able to cope with snow – and also snow melting agent on the roads! When the snow melts on unsurfaced roads it can turn to mud. If there is a lot of mud, will the suspension be adversely affected? And what about if there are ruts and grooves on the road?
It’s the job of OPQD to confirm that Nissan cars are up to the challenge of all these localized circumstances, and in their PSQC test drives they check this through routes filled with the scenarios facing Russian drivers every day.
Car washes in Russia are also different and require special attention. They use water pressure higher than in other countries (up to 35Mpa) and strong alkaline shampoo (up to pH of 14) to remove the dirt and grime of Russian roads. To check even this, Stewart Taylor’s team will clean the vehicles at the end of the day’s PSQC test drive in just the same way as a regular Russian driver would.
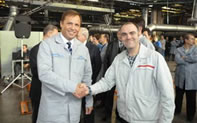
Stewart Taylor (right) meets with members of his global “orchestra.”
After all, real quality means providing customers with exactly what they want. The OPQD validate that every new car meets the expectations of even the most discerning of customers through the strict rules of Nissan’s Alliance Vehicle Evaluation Standard (AVES).
The challenges for the OPQD lie in the elaborate and diverse nature of Nissan’s business. How can the conductors possibly hope to maintain harmony with such a massive orchestra?
For Stewart Taylor, success lies in the personal touch. “I establish a strong working relationship and mutual understanding with the key people for each part of the process,” he explains. “This means that in times of need I can draw on everyone’s combined skills to best effect.”
The very best conductor surely knows every musician in his or her orchestra personally, and also how important they are to overall sound of the symphony.
Stewart Taylor is creating remarkable “music” attuned to the thinking of the customer in Europe. In fact, though, there are other OPQD based in each region and doing this kind of work all over the world today.
Stop for a moment and listen. When every musician and every element in the orchestra is consistently in tune, the melody is magnificent.