The Detectives
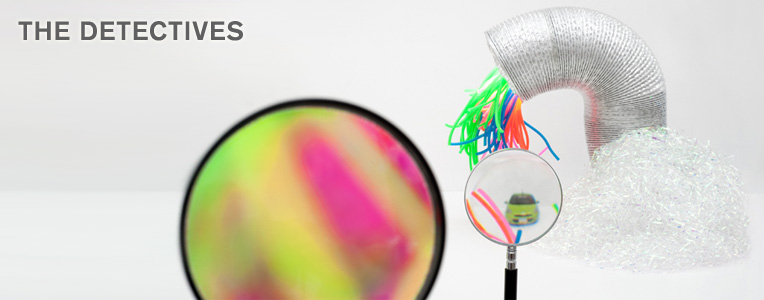
At Nissan's seven Field Quality Centers around the world, engineers work tirelessly to find faults, and fix them.
The walls of the room are covered with facts, figures, graphs and grainy photographs of the scene of the crime, and on tables around the walls lie burned-out air cleaners, upholstery that has turned to powder, and engine parts cut in half so their innermost workings can be inspected.
But this is not the operations room of the local police department, but rather the entrance hall to Nissan's Field Quality Center.
The shocking exhibit of 30 or more broken or faulty vehicle parts and components are on display for anyone to view. Not only suppliers, but any visitor is free to browse a collection that puts much that Nissan has to regret over the years on show for all the world to see.
The thinking behind such transparency comes from Nissan's firm conviction that they must never make the same mistake twice
Of course, it is a huge problem that errors were made in the first place. But what is even more important is what happens next. How to deal with the problem swiftly, and put things right. And more, how to ensure that new models will not be subject to the same mistakes.
When a vehicle with a fault is sent to the center, the staff will gather together to inspect it. These are the FQC "detectives". They go through every single possibility, one by one, however small and irrelevant it might seem, to find the cause of each problem.
The faulty part is placed in a real vehicle, recreating the actual situation where the fault occurred as closely as possible, and the center staff, suppliers, development and manufacturing teams work together to find the cause of the problem, and fix it.
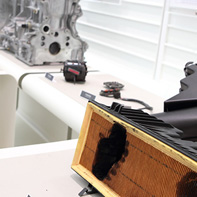
Faulty parts on display in the FQC lobby underline Nissan's firm conviction that they must never make the same mistake twice.
This process of asking "Why?" over and over is called Field Tree Analysis (FTA). Nowadays FTA is done on computers, but it used to be done on paper, and the resulting "tree" could sometimes be as large as several square meters in area.
There are times when the problem seems unsurmountable. For example there was a model that was sent to South America that had trouble starting. It was manufactured in Asia, and exported to several countries, but only in one was there a problem. What was happening to cause problems only there...?
The cause, it turned out, was the rain. Noise from the wipers, which should have had no relation at all to the starting mechanism, was damaging the diodes in the starting system, and causing it to fail.
Like detective work, it takes combing through all the endless possibilities in painstaking detail, and working with every relevant department and supplier, to find the cause of such apparently illogical faults.
The Japanese word "kaizen" has become a world standard for the philosophy of continuous improvement, and the staff at the seven FQCs around the world know that there is no end to their Quality Kaizen.
But the ultimate goal is vehicles with no faults at all, and to that end the detectives are constantly tracking down the culprits, and catching them one by one. At FQC, this determination to achieve the utmost quality, they believe, is the key to maintaining the customers' trust.
LIKE DETECTIVE WORK, IT TAKES COMBING THROUGH ALL THE ENDLESS POSSIBILITIES IN PAINSTAKING DETAIL.
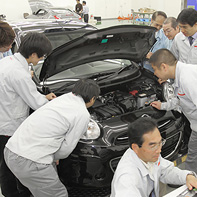
At FQC, the center staff, suppliers, development and manufacturing teams work together to find the cause of the problem, and fix it.