The Scope of Field Quality Investigation and Analysis
To accurately respond to the market's needs, we collect large numbers of parts. Everyone works as a team to thoroughly investigate the problem.
Prompt establishment of countermeasures
The first step in FQIA is to collect as many faulty parts from the field as possible. After validating the condition of each part, we attempt to replicate the problem and determine its cause. Finally, we carry out a joint analysis* using the most reliable methods possible. Once the cause is determined, we begin specific countermeasures.
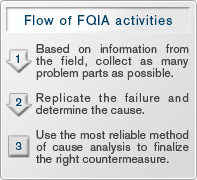
- Joint analysis involves gathering all parties dealing with the creation or maintenance of the problem part-including suppliers-and having them collectively study the cause of the problems to identify the best countermeasures.
Four Areas and Phases of Work
The FQIA area is divided into four sections: parts control, parts investigation, vehicle investigation, and joint analysis. In the course of regular quality improvement, the workflow follows that pattern as detailed below.
STEP1
Parts Control
The many parts collected from the field are sorted by category, checked against the vehicle, and then stored.
STEP2
Parts Investigation
The parts are inspected individually to confirm if they are in fact defective and to help discover the reason they failed. Statistics are kept. Defects such as scratches and paint defects on exterior parts can be judged with the naked eye. Electrical parts, however, must be checked using various devices to determine if the problem can be replicated.
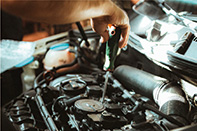
We inspect the parts individually using various devices, and replicate the problem.
Why collect as many parts as possible?
Collecting large quantities of parts that consistently cause the same problem makes it easier to determine the cause and frequency of the trouble. It also makes it easier to understand the conditions where customers are experiencing the problem. This feedback is used to produce better cars.
STEP3
Actual Vehicle Investigation
In cases where it is extremely difficult to replicate a defect, the collected parts are installed on an actual vehicle to replicate the conditions under which the problem occurred. This investigative method is common when approaching problems with engines and drivetrains.
Rigorously reproducing conditions causing defects by practicing the “three gen” principle (genba, genjitsu, genbutsu)
The actual vehicle inspection section has a vibration room that can simulate various types of road and environmental conditions. Every effort is made to replicate the actual driving conditions to reproduce the defect. In cases where the phenomenon cannot be clearly understood, we return to the customer. For example, in cases where the sound of the engine raises concern, the actual operating conditions of the customer's vehicle are replicated and an actual vehicle is put through these conditions. However, in many cases replicating the exact conditions is simply not possible. In actual vehicle inspection, various methods are used to confirm the facts.
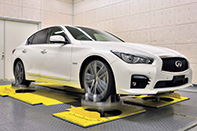
When necessary, we install the collected parts on an actual vehicle to replicate defects.
STEP4
Joint Analysis
This is where suppliers and relevant functions within Nissan collectively discuss problems confirmed during our investigations of parts and actual vehicles*1. The actual defective parts are inspected up close, the team agrees on the facts presented, and then comes up with an analysis of the cause. Finally, the team decides on what countermeasures to take. As part of the quality assurance process, Nissan also employs scientific methods such as fault tree analysis (FTA) and failure mode and effect analysis (FMEA).
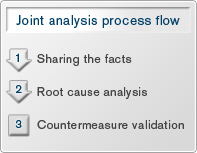
- Relevant functions in Nissan include the Development, Manufacturing, Field Quality Improvement (FQI) and Field Quality Assurance (FQA) groups.
The significance of joint analysis
Much like a relay race, each section performs operations that are linked with those of other sections. Without this kind of close cooperation, a prompt response to the customer's concern is not possible. While IT-enabled remote conferencing can speed up response, Nissan believes face-to-face meetings are still necessary and more effective. As such, when everyone involved in a problem related to a defective part is gathered, the actual parts are studied, highly reliable methods are employed in their analysis, and the causes are quickly determined, leading to the prompt implementation of countermeasures.
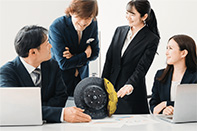
Gathering those involved in a problem related to a defective part together to discuss the matter helps us quickly determine the causes and implement countermeasures.