精度を高めた開発技術
「製品品質の設計技術・評価技術」
お客さまからの声にもとづく新車・新技術の開発
日産の開発部門では、日産車に対するお客さまからの反響を把握するために、開発担当者が日産車を保有しているお客さまにご指摘やご不満を直接伺う機会を定期的に開催しています。特に新たな性能機能・操作については、開発担当者が開発の狙いをお客さまに直接説明し、お客さまの期待に応えられていない性能機能・操作については、早急に改善するとともに新車の開発に反映させるなど、お客さまの声から得られた反響を新車・新技術の開発に活かしています。
あらゆる使用環境に応じた耐久品質の開発
近年、自動車の平均保有期間は長期化しており、耐久品質に対するお客さまの期待値は年々増しています。日産では耐久品質の適正をできる限り早く把握するために、お客さまから直接伺ったご指摘やご不満の声に応えるだけでなく、中古車調査や実車走行評価を継続して実施しています。また、世界中のお客さまの使用環境で安心して日産車を使用いただけるように、高温多湿、極低温、塩害、標高、登坂などの走行環境に応じた耐久品質を評価しています。中古車調査や実車走行評価から得られた知見は、新車や新技術の耐久品質の設計基準や評価基準に反映し、定期的な改定に活かしています。
品質設計基準・評価基準のノウハウ蓄積のエキスパート集団
品質設計技術を開発し、設計標準をストック
お客さまから頂いたご指摘やご不満に対して個別の品質向上を繰り返しても、継続的かつ網羅的に品質向上することはできません。日産では品質向上のノウハウ蓄積こそが品質問題の根本的な解決につながると考え、この10年間に渡り品質設計技術の開発に注力してきました。
パワートレイン、車体、シャシー、内外装部品、電子電装部品など各技術領域のエキスパートは、日産車の品質技術課題に対する根本的な要因を分析し、抜本的な品質向上策となる品質技術ソリューションを開発する取り組みを継続的に推進しています。品質技術課題は、世界中全ての日産車における故障修理情報を統計的に解析することで網羅的に選定されます。また、日産車を購入したお客さまに対してアンケート調査を実施し、使い勝手や操作性に関する品質技術課題を抽出しています。

使い勝手や操作性の向上
センターコンソールにはカップホルダ、シフトレバーやさまざまなスイッチ類が配置されており、その配列は使い勝手や操作性に寄与します。日産では、運転中でも直感的にカップホルダに手が届くように人間工学にもとづいたカップホルダのレイアウト基準を定めるなど、使い勝手や操作性の向上に努めています。
また、運転中に頻繁に操作するスイッチは、ステアリングスイッチに集中的にレイアウトし、直視しなくても直感で操作できるように、スイッチの形状や段差、大きさ、配列を工夫して設計しています。
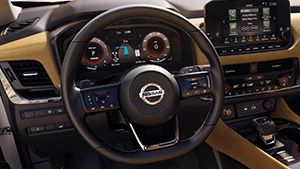
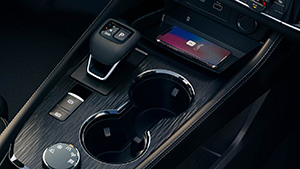
シフトレバーやステアリングの信頼性保証基準
自動車の保有期間は年々長期化する傾向にあり、耐久品質の重要性が増しています。そこで日産では、走る・曲がる・止まるといった基本性能に対する耐久品質だけでなく、お客さまが直接手に触れるインテリアの耐久品質についても重視しています。シフトレバーやステアリングなどの表皮やメッキについては、自動車の保有期間においても見栄えや操作感が劣化しないように、自動車の保有期間を想定した耐久品質の設計および評価試験を実施しています。
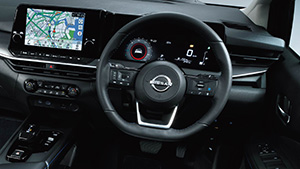
どんなに小さな品質問題でも見落とさない日産の品質チェック体制
日産独自のデザインレビュー体系
デザインレビュー(DR)とは、部品やシステムの品質をチェックするための設計審査のこと。日産では独自のDR体系を構築しており、設計のエキスパートが各部品の潜在的なリスクを徹底的に洗い出し、品質問題を未然に防ぐ工夫を盛り込んでいます。近年は電動化や知能化、コネクティドカーに関連する新技術が拡大しており、各専門技術領域におけるレビューの強化を進めています。世界で初めて採用、もしくは日産として初めて採用する新技術に対しては、FMEA(Failure Mode and Effects Analysis)を問題予見のツールとするFull Process DRを適用し、既存技術に対しては、DRBFM(Design Review Based on Failure Mode)を変更点リスク特定のツールとするQuick DRを適用しています。また、日産ではDRを設計構想段階から量産開始までの一貫した活動としており、設計、実験、生産の各部門のエンジニアが連携し、重要管理特性のばらつき抑制や工程管理までを網羅するように運用しています。
資格認定制度によるグローバル人材育成
新技術の品質問題を未然に防止するためには、DR体系を整備するだけではなく、それらの仕組みやプロセス、標準ツールを正しく理解し、実行できる人財を育成しなければなりません。日産ではDRに関する資格認定制度を通じた人財育成プログラムを構築し、グローバルに展開しています。現在、グローバルで150名を超えるDR レビューアが認定され、活躍しています。
電子・電装回路、ソフトウエアの検証
近年のクルマの多機能化により、電子・電装部品の回路は非常に複雑になっています。日産では電子・電装部品に関する品質問題を未然に防止するため、開発の初期段階において、クルマに実装する全ての電子・電装回路の試作モデルを作成し、動作を検証しています。この検証フェーズはEIPF※と呼ばれており、どのような操作をしても想定通りの動作をするように、誤作動がないか、さらには同時に操作をした場合や、通常以上の操作をした場合に意図通りに動作するかなどを確認しています。
※EIPFとは、Electric
Integration
PlatFormの略。電子・電装部品の複雑な回路においても、ソフトウェアバグを見落とさない日産独自のチェックシステム。
再発防止の仕組み
日産では、これまでに市場で発生した全ての品質問題に対して根本的な要因を分析・究明し、再発防止策の構築につなげています。開発・生産部門は、直接的な要因だけでなく、そのきっかけになった根本要因を技術面と仕組み面で究明します。続いて、品質部門が再発防止策を包括的・客観的な視点でレビューすることで、より強固な再発防止策を決定しています。また、全ての品質問題に対してもれなく再発防止策を洗い出すために、振り返りの視点を全社で統一して運用しています。
同様の品質問題が他車種や後続の新車で再発することがないように、再発防止策の決定および水平展開までの日数を厳格に管理しています。これにより、後続の新車に再発防止策を迅速にフィードバックし、類似問題の未然防止につなげています。
再発防止策の検討プロセスで得られた教訓については、社内で定められた基準帳票に蓄積して全社に展開することで、永続的な再発防止に努めています。
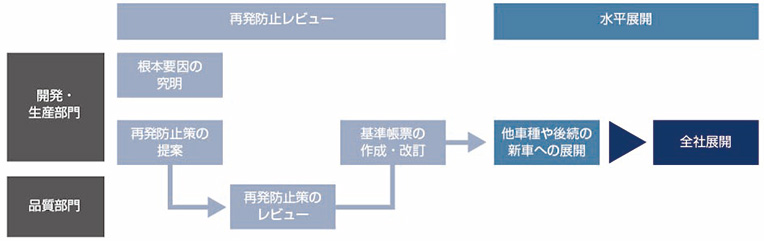