確認を重ねる生産工程
あらゆる工程に、チェック機器を導入
人間の目では判別できない細かなミスも、見逃しません
レーザーセンサーを導入して、ボディチェック
クルマとしてのカタチができ上がっていく段階で少しでもズレが生まれると、完成したクルマの品質に影響が出てきます。日産では、組立の各段階でレーザーセンサーを導入しています。例えばドアとドア枠の間にレーザーを照射すると、その隙間や段差を瞬時に測定し、品質基準から少しでも外れているとシステムが自動判定します。こうした細部のチェックを重ねた結果、正確に組み上げられた美しい合わせ面を持つクルマだけが、お客さまに提供されます。
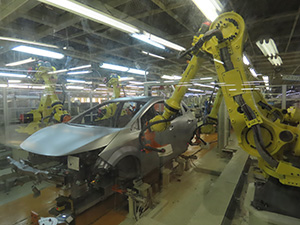
ロボットが決められたポイントの隙間や段差を
瞬時に測定し、判定する
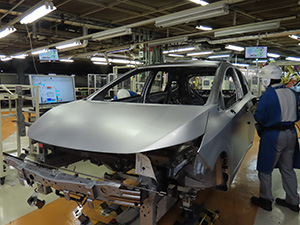
人による測定も全て電子化して測定結果を一括管理
キズやゴミを浮き上がらせる照明のもとで、塗装チェック
塗装のチェックでは、0.3mmという非常に細かなゴミまで100%検出するロボットが採用されています。光の照射の仕方を変えると塗装の変化が非常に発見しやすいことを利用して、クルマの端から端までを1台ずつ入念にチェックしていきます。検査結果は集中管理システムに瞬時に転送され、検査員は腕に装着したスマートフォンで検査結果を把握できます。
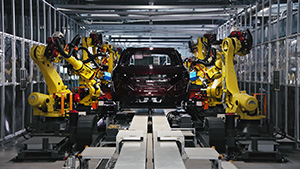
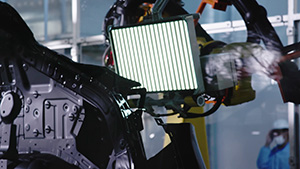
ロボットが1台当たり累計約6,000箇所を徹底的に点検する
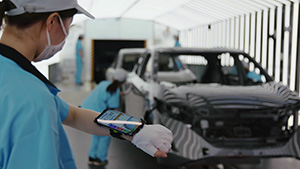
腕に装着したスマートフォンで検査結果を把握し、修復作業を行う
常にお客さま視点で判断し、安全で高品質な車両を提供します
IoTによる品質保証管理システムを構築
検査装置が各項目を自動判定することで人による誤判定を防止し、品質基準をクリアしたクルマだけを出荷するシステムを構築しています。またタブレットを導入することで検査結果を自動で記録し、全てを電子化することでトレーサビリティを強化しています。

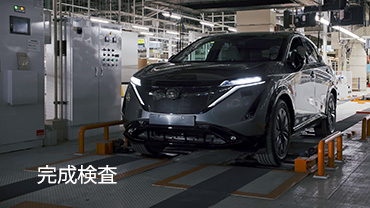
検査装置が各項目を自動判定し、人による誤判定を防止
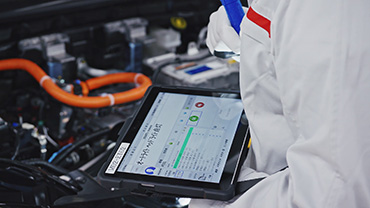
タブレットを導入し、全車の検査履歴を一括管理