電気自動車用リチウムイオンバッテリー
高密度な電極材料とパック構造の工夫で実現した大容量リチウムイオンバッテリー
日産は長年に渡り、電気自動車(EV)のキーとなるリチウムイオンバッテリーの開発に取り組み、量産型EVのパイオニアとして2010年に初代「日産リーフ」を発売しました。以降、高い信頼性はもとより、その性能を進化させつづけています。
リチウムイオンバッテリーは、鉛酸バッテリーやニッケル水素バッテリーと比べてエネルギー密度が高いことが特長です。同じ量の電気を蓄えるのであれば、バッテリーのサイズを小さくすることができます。
日産のリチウムイオンバッテリーは、リチウムイオンを高密度に蓄えられる電極材料と車種ごとに適切なパック構造により、大容量化を実現しています。
技術の仕組み
正極材料
初代「リーフ」ではマンガン系正極材料を採用していましたが、三元系正極材料に進化させ、高いエネルギー密度を実現しています。
三元系正極材料は層状構造のためリチウムイオンを高密度に蓄えることができ、バッテリーの大容量化に貢献します。
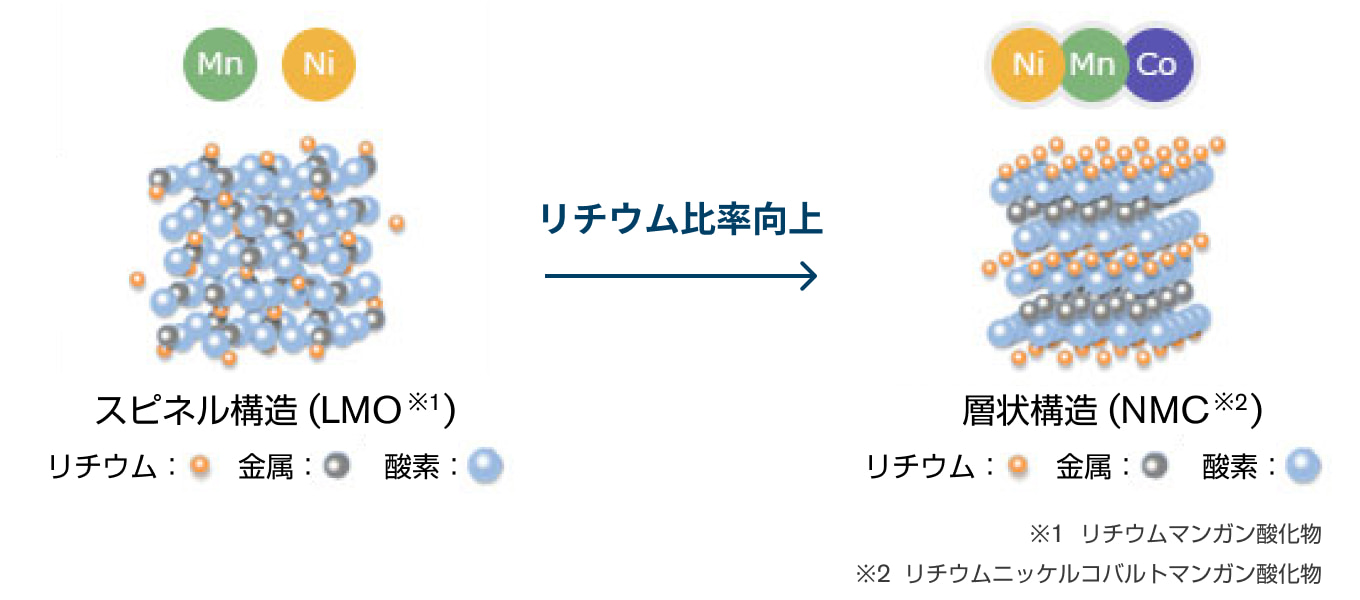
パック構造
パック構造には、さまざまなプラットフォームにフレキシブルに対応する「ユニバーサルスタック構造」と、CMF-EVプラットフォームに対応する「フラットバッテリー構造」を導入しています。
1. さまざまなプラットフォームに対応するユニバーサルスタック構造
バッテリーセルは高い冷却性能とシンプルな構造を特長とするラミネートセルを用います。従来はこのセル8枚で1つのモジュールを構成していましたが、高さの調節が8セル単位でしかできないため搭載レイアウトには限界があり、スペースを十分に活用しきれていませんでした。そこで、セルの枚数を自在に変えることができ、レイアウトの自由度をさらに高めるユニバーサルスタック構造を開発しました。セルの接合部にレーザー溶接を採用することでセルの積層枚数を自在に変えて車両形状に合わせた最適なモジュール高さとするとともに、モジュールの全長も短くすることができます。
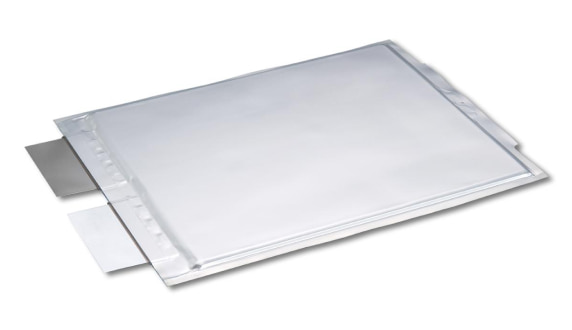
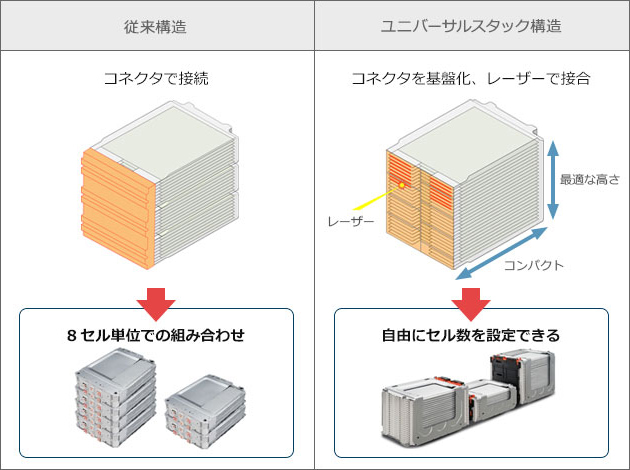
例えば、フロア下のトンネルスペースを活用し、広い室内空間を維持しながら大容量のバッテリーを搭載することが可能です。
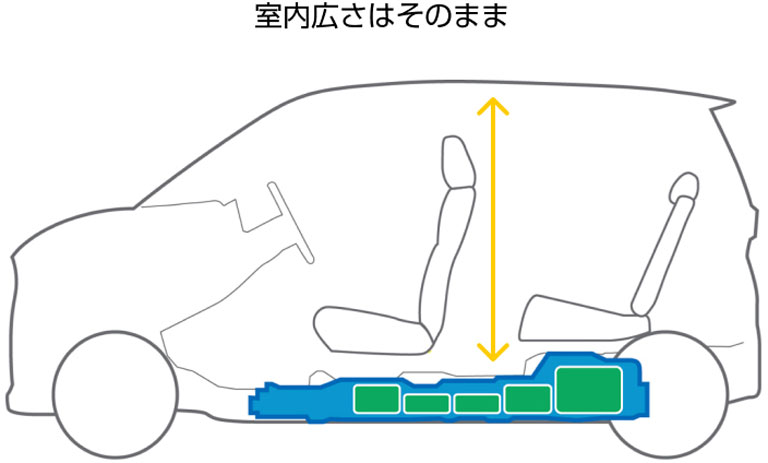
2. CMF-EVプラットフォームに対応する大容量フラットバッテリー構造
大型モジュールを搭載したフラットバッテリー構造を採用し、十分なバッテリー容量を確保しながら、フロアがフラットですっきりとした足元空間を実現します。
フロアのフラット化と大容量化
通常、車体には強度や剛性を高めるために必要なクロスメンバーという骨格部品があり、フロアを横切るように設置され、フロアに凹凸が生じてしまいます。
この構造ではパックの剛性を上げるとともにフロアとの締結点を最適設計することで、凹凸の少ないフラットなフロア面の実現が可能となります。さらに、バッテリーセルを効率的に搭載することができる大型のバッテリーモジュールを採用することで大容量化も実現しています。
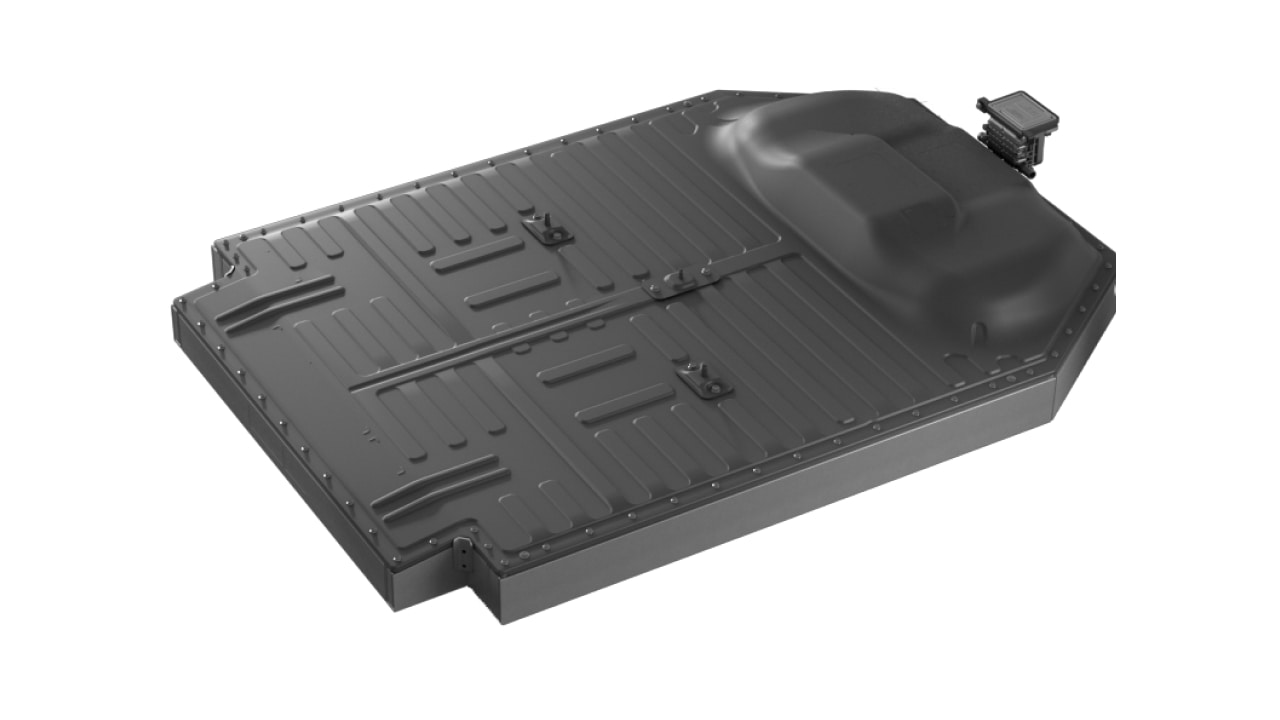
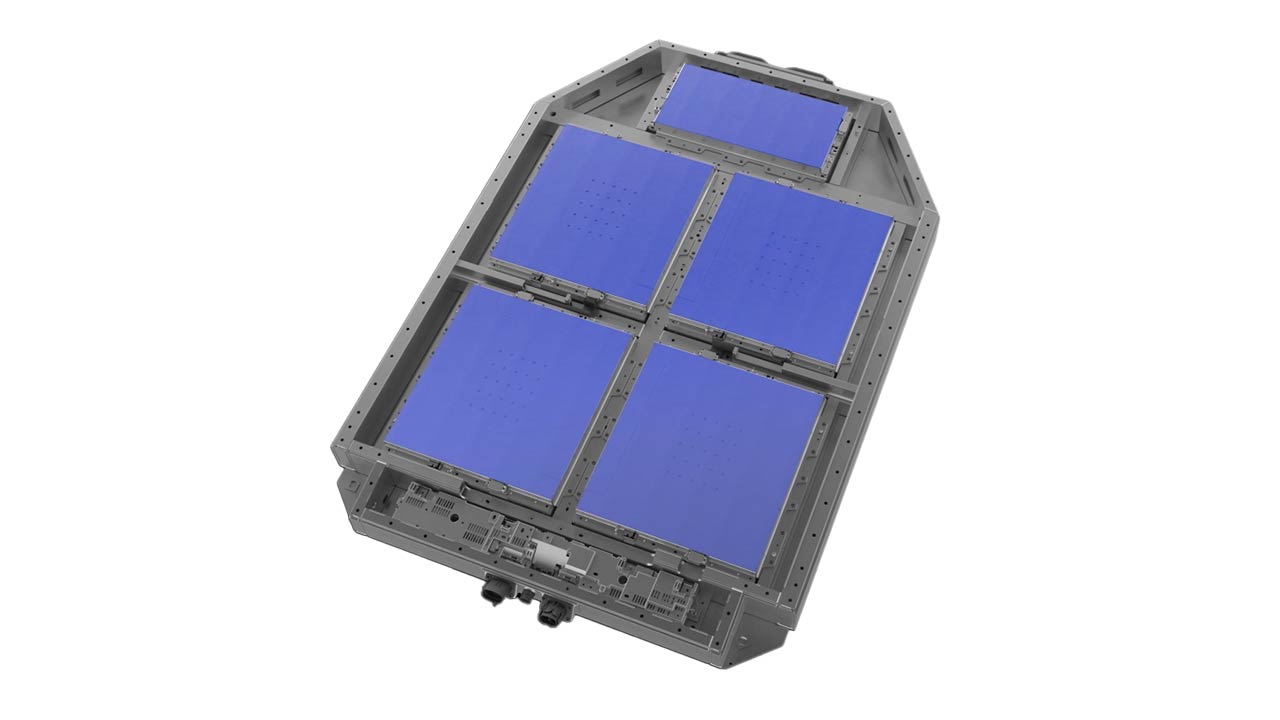
第3世代「リーフ」のバッテリー
薄型の温度調整構造
パックの底面全体に冷却水の流路を設けることで、薄型形状を保持したままバッテリーを均一に冷却および加温することができる構造とし、シーンに応じた適切な温度に調節します。
さらに第3世代「リーフ」では、バッテリー下の車体アンダーカバー形状の工夫により空気の流れを遮ることで断熱性を高め、より少ないエネルギーですばやく適切な温度に保ちます。
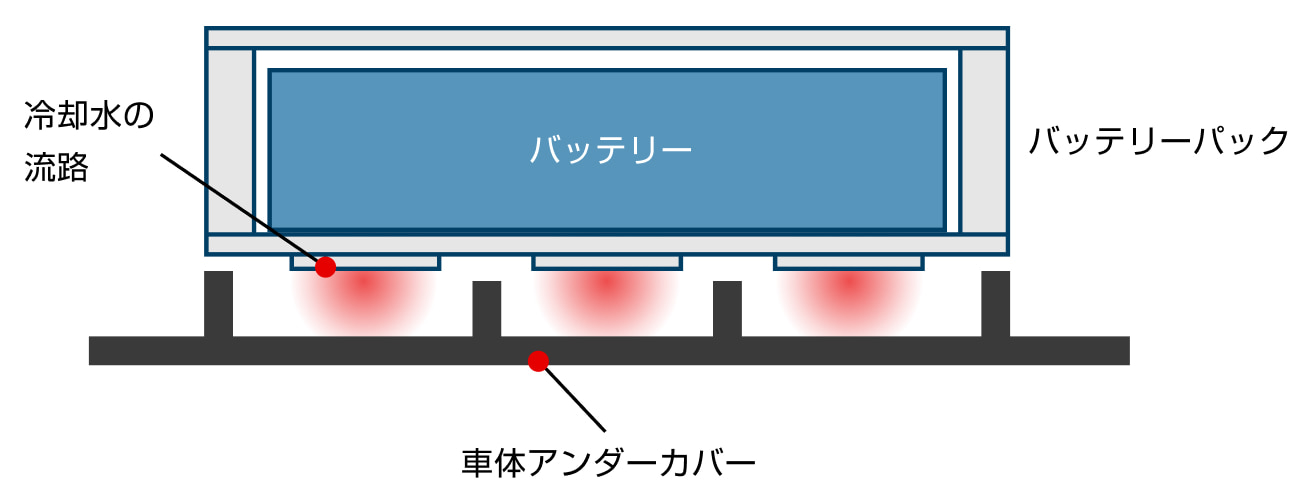