Nissan Passionate Challengers
EPISODE 01
EVの心臓部である
モーターを高品質に
量産する工夫
横浜工場 第一製造部 アクスル・電動パワートレイン課 田中喜之さん
わずかな傷も見逃さない
世界初の量産EVである日産リーフをはじめ、セレナ、キックス、ノートなどのe-POWER用、さらにスカイラインなどハイブリッド用のモーター製造を担うのが、横浜工場のアクスル電動パワートレイン課だ。責任者の田中喜之は、初代日産リーフのモーター製造から関わるベテランスタッフである。
「モーターに使っているコイル線は、皮膜にわずかな傷がつくだけで商品になりません。そのために設備から運搬まで、あらゆるところに気を使った設備設計をするところから、モーターづくりは始まっているのです」
01. コイルを巻き取る
02. アッパーツールに巻き取ったコイルをステーターコアに挿入しているところ
03. ガラスチューブを手作業で組み付け
04. 電気回路ごとにコイル束をそろえる[配策]
05. コイルエンドを潰し寸法を出す[最終成形]
06. 白い糸を縫い込む[レーシング]
07. 端子を取り付ける[ヒュージング]
08. 絶縁ワニスをコーティングしハウジングに焼嵌める
09. ローターとステーターを組み合わせる
10. センサーを組み付け、最終検査をして完成
そんなモーター製造に関わるスタッフは、約130名。モーター製造は3ラインが稼働し、そのうちひとつはノート専用だ。「横浜工場製のモーターは、永久磁石を組み込んだ回転体を作っていますので、磁石が影響を受けにくい設備を使うことが重要です。ステンレスやアルミを使って磁気を帯びないようにしたり、樹脂を使って傷がつかないようにしたりといった工夫をしています」
進化する技術と製造工程
初代日産リーフのモーター製造に関わり始めた当初は、試行錯誤の連続だったと田中は言う。
「最初の製造ラインはお試しのようなもの。まずは量産よりも、パフォーマンスを出すことを目指しました。その後、2012年に量産体制に入り、徐々に車種もモーター生産数も増えていきました」
そうして時間をかけてモーターの安定供給を実現すると、日産の技術はさらに進化。それによる変化は製造工程にも現れた。
「モーターの中核となるステーターコアという部品があります。鉄の芯のことで、これにコイルを巻くのですが、2012年から寸法が約20%(140mmから115mmに)薄くなりました。それに伴い、巻きつけるコイルを2%(108本から110本に)増加。芯自体は薄くなっても巻き数が増えるのでパフォーマンスは変わらないということです」
また組立工程も進化。例えば前述の永久磁石は、磁化させたものを組み込むのではなく、組み込んだ後に磁化させるようにした。
「磁石にタッチする時間が短くなるし、S極とN極を逆につけるミスもなくなります」
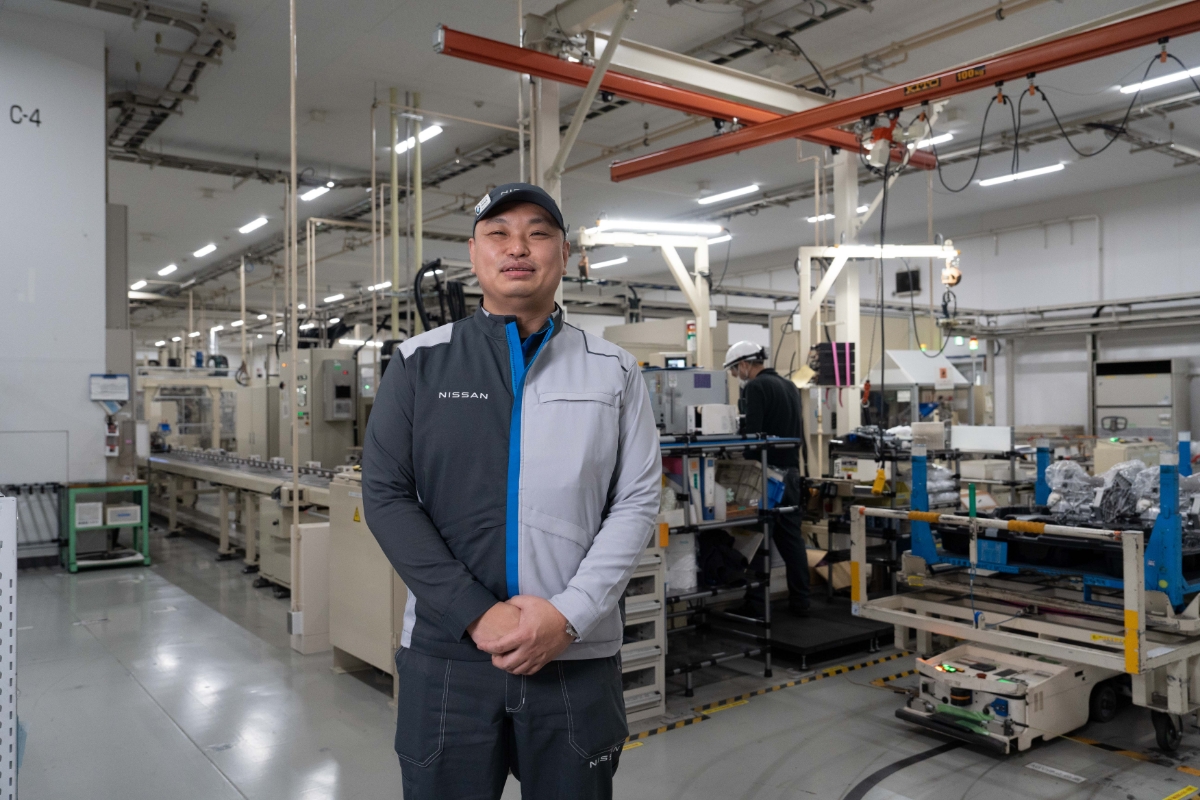
創業の地でのものづくり
最先端技術を詰め込んだモーターを製造する工場の設備もまた、先端化が進む。田中は「現在、人が担当している製造工程も、やがてオートメーション化するでしょう」と言う。
「自動化できるところは自動化した方がいいと思います。人はミスをしますからね。でも、最終的に確認するのは人です。その意味で知識を持ち、経験を重ねた人材を育成することも我々の使命だと思っています」
その背景にあるのは、横浜が創業の地であるという誇りだ。
「横浜工場は『パイロットプラント』という位置づけにあり、これは量産体制の基準をつくるということです。だから私自身、新しい技術の検討会議に出て、試作の現場に行き、情報を得るようにしています。そうすることで稼働中の製造現場では得られない情報をつかみ、伝えていく。それが新しい技術を搭載したクルマを作る準備につながっていくと思うのです」
創業の地・横浜では、最先端のモーターが作られると共に、日産ならではのものづくりにこだわる人材育成も行われている。