1台ずつ生産する組立工程に対してプレス部品や樹脂成型部品など段取り作業を伴い一定数量のロット生産を行う工程において、後工程である組立工程が翌日必要とする量だけを生産する方式を「いるだけ生産」と呼んでいます。
プレス工程などで比較的多く採用されている「在庫補填生産」は在庫がある一定量まで減ったときに決まったロットサイズで生産するため「不定期定量」という方式になりますが、いるだけ生産は翌日必要な量を生産するので「定期不定量」という方式になることが特徴のひとつです。弊社においても従来はプレス工程の生産は数日先の内示を見て一定数まで在庫が減ったときに大きなロットサイズで生産する在庫補填生産を採用していましたが、種々の要因から必要以上に前倒しで生産する場合があり在庫の山を築き上げることとなっていました。
いるだけ生産の狙いは、つくり過ぎによる在庫過多を抑制することであり、また在庫を見ながら見込みで生産計画を立てるといった間接工数を削減することも狙っています。この方式は後工程からの日々の要求量がある程度平準化されており、翌日の生産量が確定していれば(厳密な受注確定でなくても)生産ロットの異なる連続した工程で適用可能です(プレス工程→溶接工程、樹脂成型→組立、など)。
いるだけ生産を実現していくためには、後工程が1日に消費する全品種を前工程も同様に1日で生産する必要があり、前工程の段取り時間を短縮することが主要課題となります。まずは現状の生産運営の基礎データを収集し生産スペック表(図1)に整理します。プレスや樹脂成型の各設備についてどの部品をどれだけ生産しているか、段取りや不良などのロスがどれくらい発生しているかを月単位で把握することで定量的に課題を捉えることができ、改善テーマ設定や目標設定に役立てることができます。また生産諸元だけでなく在庫量や在庫スペースなども目標項目に上がってきますので、その数値も押さえておくと効果確認の際に改善前後の比較ができます。(図1)
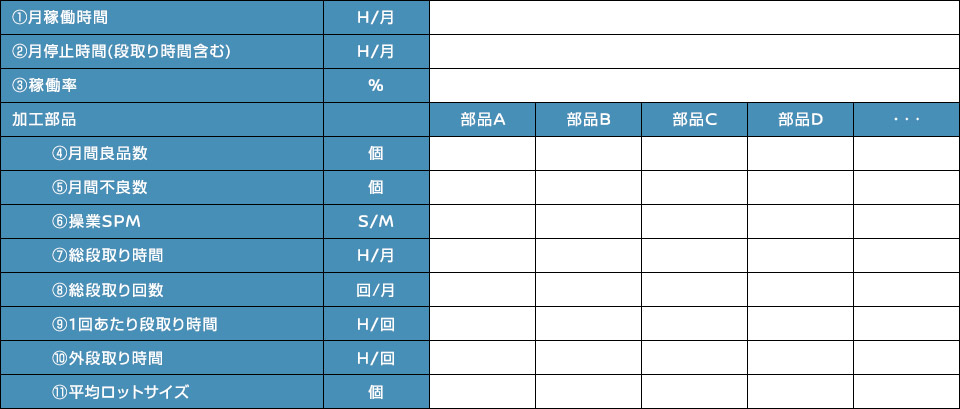
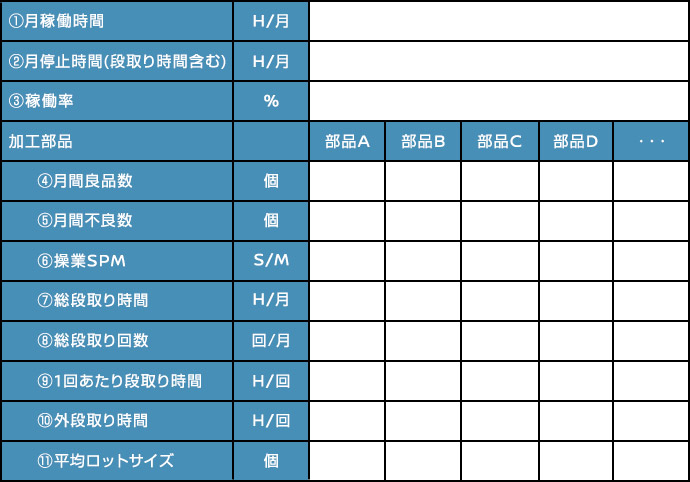
生産スペック表のデータを基に「ありたい姿」を描いていきます。ありたい姿は後工程で必要な全種類を生産することですが、実際には非量産品もあり外段取りがネックになる場合もあるので総合的な効率を考慮して現実的な目標となる「目指す姿」に落とし込んでいきます。(図2)
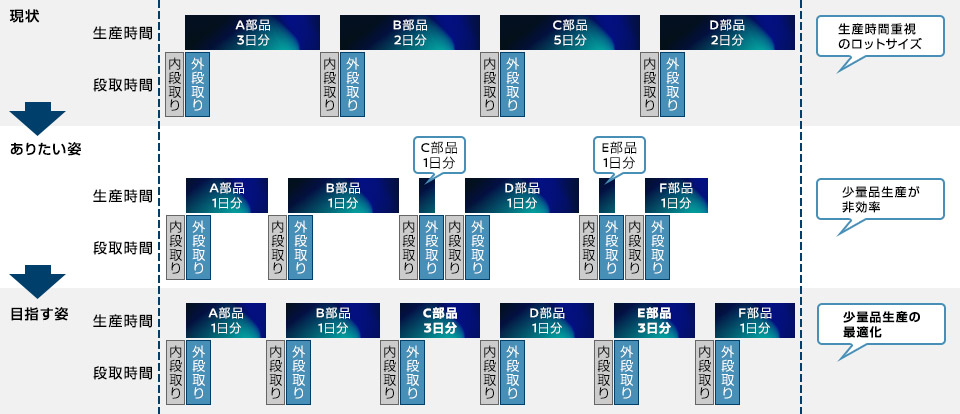
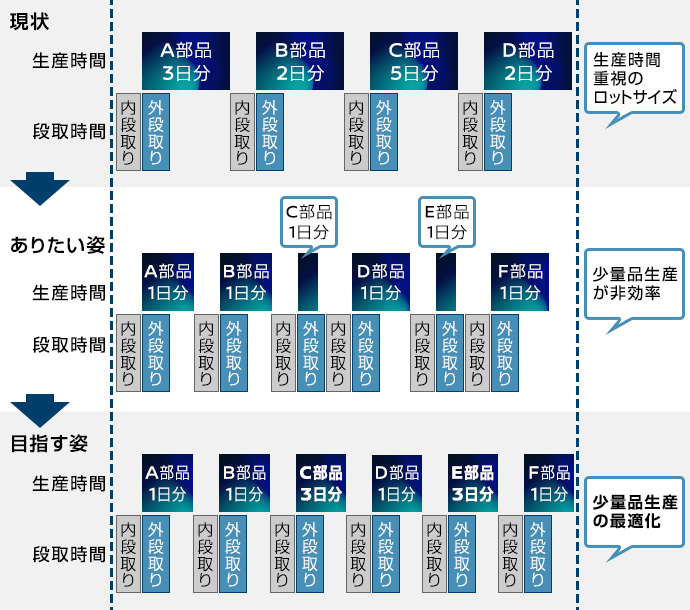
主要課題である段取り改善の具体的な進め方としては、その作業をビデオ撮影して手順と手順ごとの時間を確認し、関係者で改善案検討会を行うことをお勧めします。また段取り改善の視点は「外段取り化」や「3レス化(ボルトレス、工具レス、調整レス)」など定石と言えるものがいくつかあるので、それらを段取り手順に照らし合わせて改善案を検討していくと良いでしょう。
段取り時間以外にも不良率低減や設備トラブル低減、SPM(Stroke Per Minute=1分当りストローク数)向上といったことも改善テーマとして取り組む必要があり、改善実行計画を作成し関係部署と連携して進めていくことが重要です。それから念のために申し上げておくと、生産は「いるだけ」ですが安全在庫は設定してありますので、適正な安全在庫の設定と先入れ先出しの仕組みの構築も必須となります。
冒頭にいるだけ生産は生産ロットの異なる連続した工程に適用するとお話ししましたが、プレス、樹脂成型、ダイカストなど単一の工程で自社の生産を完結する企業においても多品種少量が常となっている昨今、取引先を次工程と捉えて在庫削減を狙ったいるだけ生産の取り組みを実行してみてはいかがでしょうか。